Warehouse Design and Operations: How to invest in your warehouse layout and operations for a more streamlined and cost-effective future, backed by real-life case studies
In today's competitive market, Australian retail and manufacturing businesses are constantly looking for ways to improve service and reduce operating costs. One key area where businesses can make significant improvements is in their warehouse design, layout, and operations. By investing in efficient warehouse management, you can create a more streamlined and cost-effective future for your business. In this article, we will explore some of the top strategies for upgrading your warehouse design and operations, specifically tailored to the Australian market, supported by compelling case studies.
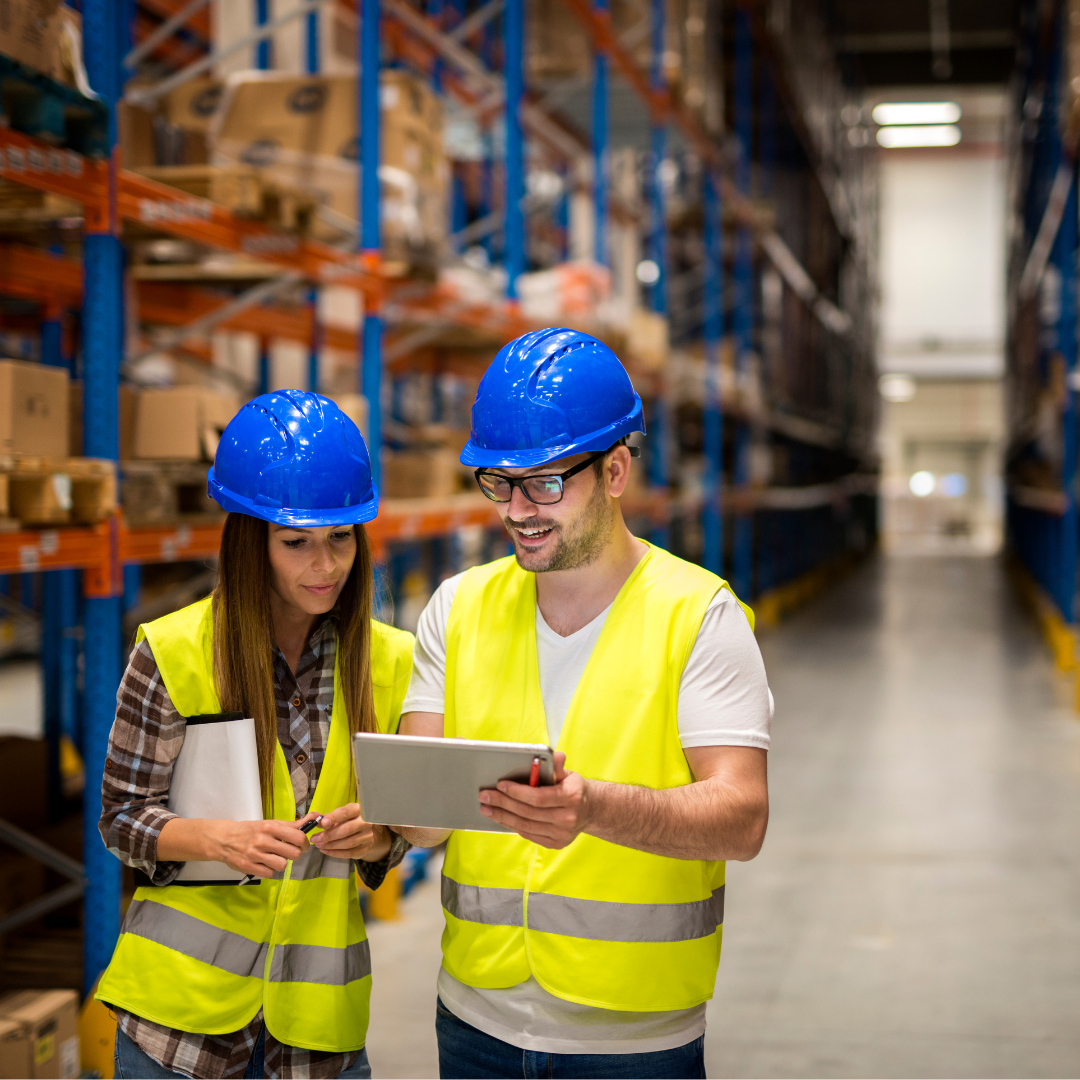
Maximise Space Utilisation
Optimising your warehouse space is crucial in reducing costs and improving efficiency. There are several ways you can achieve this:
- Implement a layout that maximises vertical space, using high-rise racking and shelving systems. In a case study by Dexion Australia, a leading storage solutions provider, an Australian-based company increased its storage capacity by 40% through the implementation of a high-rise racking system, without expanding the warehouse footprint.
- Consider narrow aisle configurations to save floor space, while still allowing forklifts and other equipment to move freely. A retail company in Sydney reported a 20% increase in storage density after adopting a narrow aisle configuration.
- Utilise mezzanine floors to create additional storage or office space, without expanding the warehouse footprint. A Melbourne-based manufacturing company added a mezzanine floor, resulting in a 50% increase in storage space and improved workflow.
Invest in Warehouse Automation
Automation can significantly improve the efficiency of warehouse operations, leading to reduced labour costs and increased productivity. Some key areas to consider for automation include:
- Conveyor systems and automated guided vehicles (AGVs) for material handling and transportation. In a case study by Dematic, an intralogistics company, an Australian retailer implemented an AGV system, reducing labour costs by 25% and increasing throughput by 50%.
- Robotic picking and packing solutions to reduce manual labour and improve accuracy. A case study by Swisslog Australia, a leading logistics automation provider, demonstrated that an Australian e-commerce company achieved a 99.9% picking accuracy rate and a 60% reduction in labour costs after integrating robotic picking solutions.
- Warehouse management systems (WMS) to streamline inventory management, order processing, and other administrative tasks. An Australian food distributor implemented a WMS, resulting in a 15% increase in picking productivity and a 10% reduction in order processing errors.
Prioritise Employee Safety
A safe working environment is not only a legal requirement, but it also contributes to increased productivity and reduced costs through fewer accidents and downtime. To ensure the safety of your employees:
- Provide proper training and safety equipment, such as high-visibility vests, hard hats, and steel-toed boots. An Australian manufacturing company reported a 30% decrease in workplace injuries after investing in employee safety training and equipment.
- Designate pedestrian walkways and enforce a clear separation between employees and machinery. A case study by an Australian safety consultancy showed that implementing designated pedestrian walkways resulted in a 60% reduction in warehouse accidents.
- Regularly inspect and maintain equipment, racking systems, and other warehouse infrastructure to minimise risks. A Perth-based logistics company saw a 20% reduction in maintenance-related downtime after adopting a proactive equipment inspection and maintenance program.
Implement Energy-Efficient Solutions
Reducing energy consumption in your warehouse can lead to significant cost savings. Consider the following energy-efficient strategies:
- Install LED lighting and motion sensors to save on electricity costs. An Adelaide-based retail company reported a 40% reduction in energy consumption after upgrading to LED lighting and installing motion sensors.
- Insulate the warehouse to reduce heating and cooling expenses. A case study by an Australian insulation provider demonstrated that a warehouse in Victoria achieved a 25% decrease in energy costs after retrofitting insulation.
- Implement solar panels to harness Australia's abundant sunlight and reduce reliance on the grid. A Brisbane-based manufacturing company installed solar panels on their warehouse roof, generating 80% of their electricity needs and significantly reducing their energy bills.
Adopt Lean Warehousing Principles
Lean warehousing focuses on eliminating waste, increasing efficiency, and reducing costs. Some ways to implement lean principles in your warehouse include:
- Standardising processes and procedures to reduce variability and increase consistency. A case study by an Australian lean consulting firm showed that a Sydney-based manufacturer experienced a 30% reduction in operational waste and a 20% improvement in overall efficiency after standardising warehouse processes.
- Using the 5S methodology (Sort, Set in order, Shine, Standardise, and Sustain) to maintain a clean, organised, and efficient workspace. An Australian automotive parts distributor implemented the 5S methodology, resulting in a 15% increase in productivity and a 10% reduction in order processing time.
- Implementing continuous improvement initiatives to regularly assess and optimise warehouse operations. A Melbourne-based food distributor embraced a continuous improvement culture, leading to a 12% increase in warehouse efficiency and a 15% reduction in operational costs.
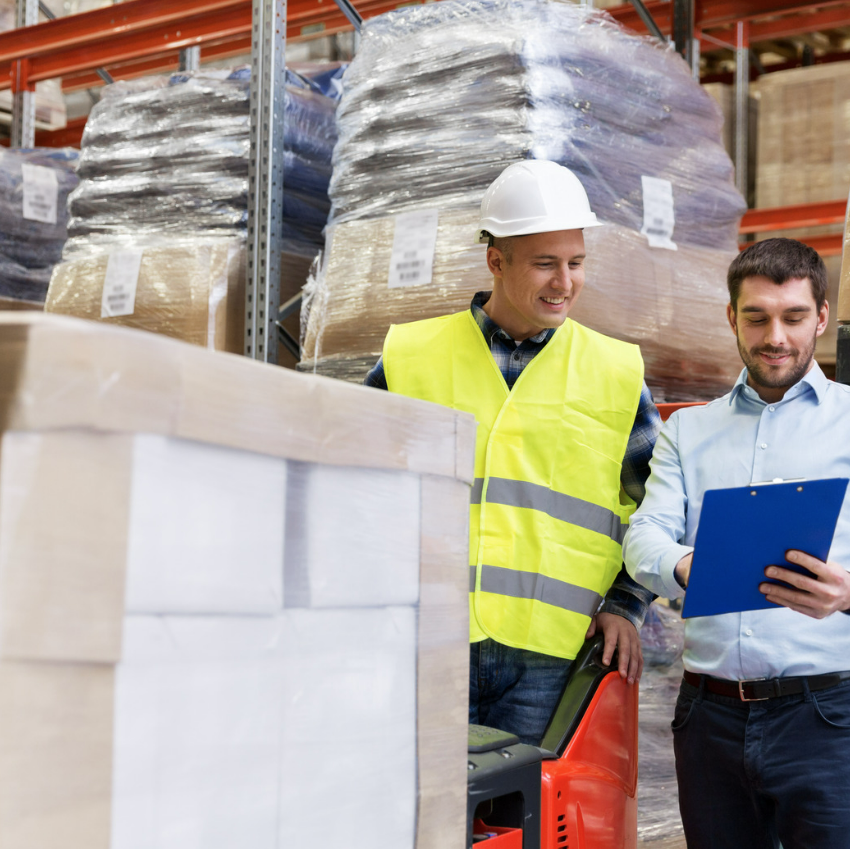
Investing in warehouse design, layout, and operations can significantly improve the efficiency and cost-effectiveness of your retail or manufacturing business. By maximising space utilisation, automating processes, prioritising safety, implementing energy-efficient solutions, and adopting lean warehousing principles, you can create a streamlined and profitable future for your Australian business. As demonstrated by the case studies shared above, real-life success stories confirm the tangible benefits of these strategies. So, start evaluating your current warehouse setup and take the necessary steps to optimise your operations today!
Contact us today, trace. your supply chain consulting partner.