Design an Efficient Warehouse Operation: A Comprehensive Guide
Efficient warehouse operations are crucial for any business involved in the storage and distribution of goods. From layout design and capacity planning to space optimisation and automation, numerous factors contribute to the overall efficiency of a warehouse. In this comprehensive guide, we’ll explore each aspect in detail, offering actionable insights to help you design and maintain a warehouse that maximises productivity and minimises costs.
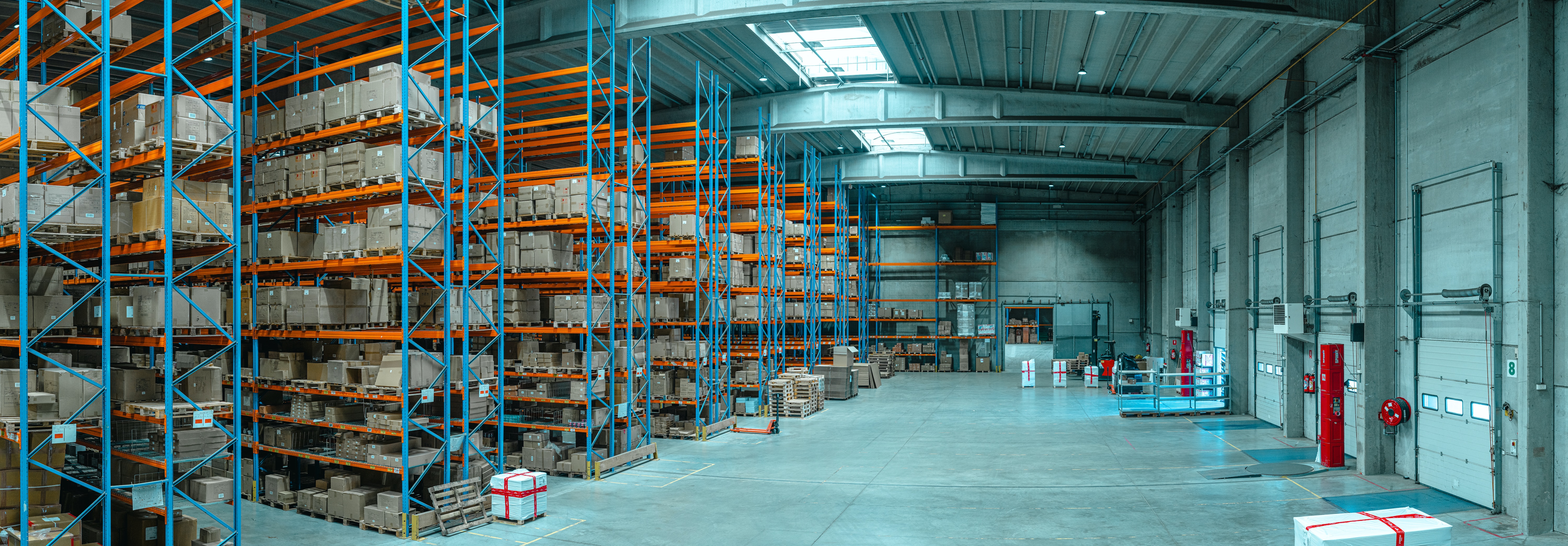
Understanding Warehouse Layout
The Importance of Layout
The layout of a warehouse significantly impacts its efficiency. A well-designed layout ensures smooth movement of goods, minimises travel time, and reduces handling costs. It also enhances safety and maximises the use of available space.
Key Elements of Warehouse Layout Design
- Receiving Area: The receiving area should be strategically located near the main entrance to facilitate quick unloading of goods. It should have ample space for staging incoming shipments and inspecting goods for quality and accuracy.
- Storage Area: This is where goods are stored until needed. The storage area can be divided into different zones based on the type of goods, their storage requirements, and the frequency of access. Common storage systems include pallet racking, shelving, and mezzanine floors.
- Picking Area: The picking area is where items are selected for order fulfilment. It should be designed to minimise travel time and facilitate quick, accurate picking. Consider using flow racks, carton flow systems, and automated storage and retrieval systems (AS/RS) to enhance picking efficiency.
- Packing Area: The packing area is where items are packed for shipment. It should be close to the picking area to reduce the time spent moving items between picking and packing. Provide ample space for packing stations, packing materials, and finished orders.
- Shipping Area: The shipping area should be located near the loading docks to facilitate quick loading of outbound shipments. It should have sufficient space for staging packed orders and conducting final inspections before shipment.
Layout Design Tips
- Optimise Aisle Width: Ensure aisles are wide enough to accommodate material handling equipment but not so wide that they waste space.
- Implement Cross-Docking: Cross-docking minimises storage time by directly transferring goods from inbound to outbound shipments.
- Use Vertical Space: Utilise vertical space with tall shelving and mezzanine floors to maximise storage capacity without expanding the warehouse footprint.
Capacity Planning and Space Optimisation
Assessing Capacity Needs
Capacity planning involves determining the amount of space required to store goods and manage warehouse operations efficiently. Consider factors such as inventory levels, turnover rates, and future growth projections.
Space Optimisation Strategies
- Slotting: Slotting involves organising inventory based on the frequency of access and picking patterns. Place high-demand items in easily accessible locations to reduce travel time and improve picking efficiency.
- Dynamic Storage: Implement dynamic storage systems that adapt to changing inventory levels and types. Examples include mobile racking, which allows racks to be moved to create temporary aisles, and vertical lift modules (VLMs), which adjust shelf heights to optimise space usage.
- Consolidation: Regularly review and consolidate inventory to free up space. Remove obsolete or slow-moving items and reallocate space to high-demand goods.
- Lean Inventory Management: Adopt lean inventory management practices to minimise excess inventory and optimise space utilisation. Techniques such as just-in-time (JIT) inventory and demand forecasting can help reduce the amount of space needed for storage.
Embracing Automation
Benefits of Warehouse Automation
Automation can significantly enhance warehouse efficiency by reducing labour costs, improving accuracy, and increasing throughput. Automated systems can handle repetitive tasks, freeing up employees to focus on more value-added activities.
Types of Warehouse Automation
- Automated Storage and Retrieval Systems (AS/RS): AS/RS systems use automated cranes or shuttles to store and retrieve items from storage racks. They are ideal for high-density storage and can significantly reduce picking times.
- Conveyor Systems: Conveyor systems transport goods throughout the warehouse, reducing the need for manual handling and minimising travel time.
- Automated Guided Vehicles (AGVs): AGVs are self-guided vehicles that transport goods within the warehouse. They can be used for tasks such as moving pallets, towing carts, and replenishing stock.
- Robotic Picking Systems: Robotic picking systems use robots to pick items from storage locations and place them into bins or totes for order fulfilment. These systems can improve picking accuracy and speed.
- Warehouse Management Systems (WMS): A WMS is a software solution that manages warehouse operations, including inventory management, order fulfilment, and shipping. A WMS can provide real-time visibility into inventory levels, optimise picking routes, and automate replenishment.
Implementing Automation
- Assess Needs: Evaluate your warehouse operations to identify areas where automation can provide the most benefit.
- Start Small: Implement automation gradually, starting with a single process or area. This allows you to test and refine the system before expanding.
- Integrate Systems: Ensure automated systems are integrated with your WMS and other warehouse technologies for seamless operation.
- Train Staff: Provide comprehensive training for employees on how to use and maintain automated systems.
Enhancing Warehouse Efficiency
Lean Warehousing Principles
Lean warehousing focuses on eliminating waste and optimising processes to enhance efficiency. Key principles include:
- Value Stream Mapping: Identify and analyse all activities involved in the warehouse operation to identify areas of waste and opportunities for improvement.
- Continuous Improvement (Kaizen): Encourage a culture of continuous improvement where employees are empowered to suggest and implement improvements.
- Standardised Work: Develop standardised procedures for all warehouse activities to ensure consistency and efficiency.
- 5S Methodology: Implement the 5S methodology (Sort, Set in order, Shine, Standardise, Sustain) to create an organised and efficient workspace.
Technology Integration
Integrating advanced technologies can further enhance warehouse efficiency:
- Internet of Things (IoT): IoT devices can provide real-time data on inventory levels, equipment status, and environmental conditions. This data can be used to optimise operations and prevent issues before they occur.
- Artificial Intelligence (AI): AI can be used for demand forecasting, inventory optimisation, and predictive maintenance. Machine learning algorithms can analyse historical data to predict future trends and optimise warehouse operations.
- Blockchain: Blockchain technology can enhance supply chain transparency and security by providing a tamper-proof record of transactions and movements of goods.
Safety and Ergonomics
Ensuring Safety
Safety is a critical aspect of warehouse operations. Implementing safety measures not only protects employees but also reduces the risk of costly accidents and downtime.
- Safety Training: Provide regular safety training for all employees, covering topics such as proper lifting techniques, equipment operation, and emergency procedures.
- Signage and Labelling: Use clear signage and labelling to identify hazards, emergency exits, and safety equipment.
- Equipment Maintenance: Regularly inspect and maintain equipment to ensure it is in safe working condition.
- Safety Barriers: Install safety barriers and guardrails to protect employees from hazards such as moving vehicles and machinery.
Ergonomic Design
Ergonomics focuses on designing workspaces and tasks to minimise physical strain and improve employee comfort and productivity.
- Workstation Design: Design workstations to minimise repetitive movements and awkward postures. Adjustable workstations can accommodate employees of different heights and preferences.
- Material Handling Equipment: Use material handling equipment such as lift tables, conveyor belts, and pallet jacks to reduce the physical strain of lifting and moving heavy items.
- Ergonomic Tools: Provide ergonomic tools such as anti-fatigue mats, cushioned floor surfaces, and ergonomic hand tools to reduce strain and improve comfort.
Sustainable Warehouse Practices
Energy Efficiency
Implementing energy-efficient practices can reduce operational costs and environmental impact.
- Lighting: Use energy-efficient LED lighting and motion sensors to reduce energy consumption.
- Climate Control: Implement energy-efficient climate control systems to maintain optimal temperature and humidity levels while minimising energy use.
- Renewable Energy: Consider installing solar panels or other renewable energy sources to power your warehouse.
Waste Reduction
Reducing waste can improve efficiency and sustainability.
- Recycling: Implement recycling programs for materials such as cardboard, plastic, and paper.
- Packaging: Use reusable and recyclable packaging materials to reduce waste.
- Inventory Management: Adopt inventory management practices that minimise excess inventory and reduce the risk of obsolete stock.
Sustainable Practices
- Green Building Design: Design or retrofit your warehouse with sustainable materials and practices, such as rainwater harvesting, energy-efficient insulation, and green roofs.
- Supply Chain Sustainability: Work with suppliers and partners to promote sustainability throughout the supply chain.
Technology to Support Warehouse Operations
Enhancing Receipting, Dispatch, Putaway, and Picking with Technology
Incorporating advanced technology is essential for optimising various warehouse operations, including receipting, dispatch, putaway, and picking processes. A robust Warehouse Management System (WMS) plays a pivotal role in streamlining these activities.
Warehouse Management Systems (WMS)
A WMS provides real-time visibility and control over inventory, enabling efficient receipting and dispatch processes. When goods arrive, the WMS can automate the receipting process, verifying quantities and conditions against purchase orders. For putaway, the system can generate optimal storage locations based on item attributes and current warehouse layout, reducing travel time and labour costs.
During picking, a WMS can guide workers through the most efficient routes, ensuring accurate and timely order fulfilment. Technologies such as barcode scanning, RFID tags, and voice-directed picking systems further enhance accuracy and speed.
Additionally, a WMS supports advanced inventory management by providing real-time data on stock levels, locations, and movements. This helps in maintaining optimal inventory levels, preventing stockouts and overstock situations. By integrating with other systems such as Enterprise Resource Planning (ERP) and Transportation Management Systems (TMS), a WMS can offer a comprehensive solution for managing the entire supply chain, from inbound logistics to outbound distribution.