As we enter 2024, the e-commerce landscape continues to expand. The unstoppable digitisation of businesses requires the adoption of modern solutions. Most competitive businesses today adopt warehouse and order management systems.
Warehouse management involves overseeing and controlling the day-to-day operations of a warehouse, including inventory management, order processing, and distribution. Once systemised, this practice ensures efficient storage and movement of goods within a warehouse. Proper warehouse management can bolster customer satisfaction and operational success in the long run.
On the other hand, order management is the process of tracking and fulfilling sales orders. It involves everything from order entry, inventory and warehouse management to shipping and ensuring customer satisfaction. Effective order management systems enable timely and accurate order processing. When orders run smoothly, you can build a better reputation through the customer's trust and loyalty.
trace. understands the importance of finding a system that aligns with your needs and goals. We can be your partner in navigating modern business challenges and finding effective solutions. Take this first step with us towards another productive year.
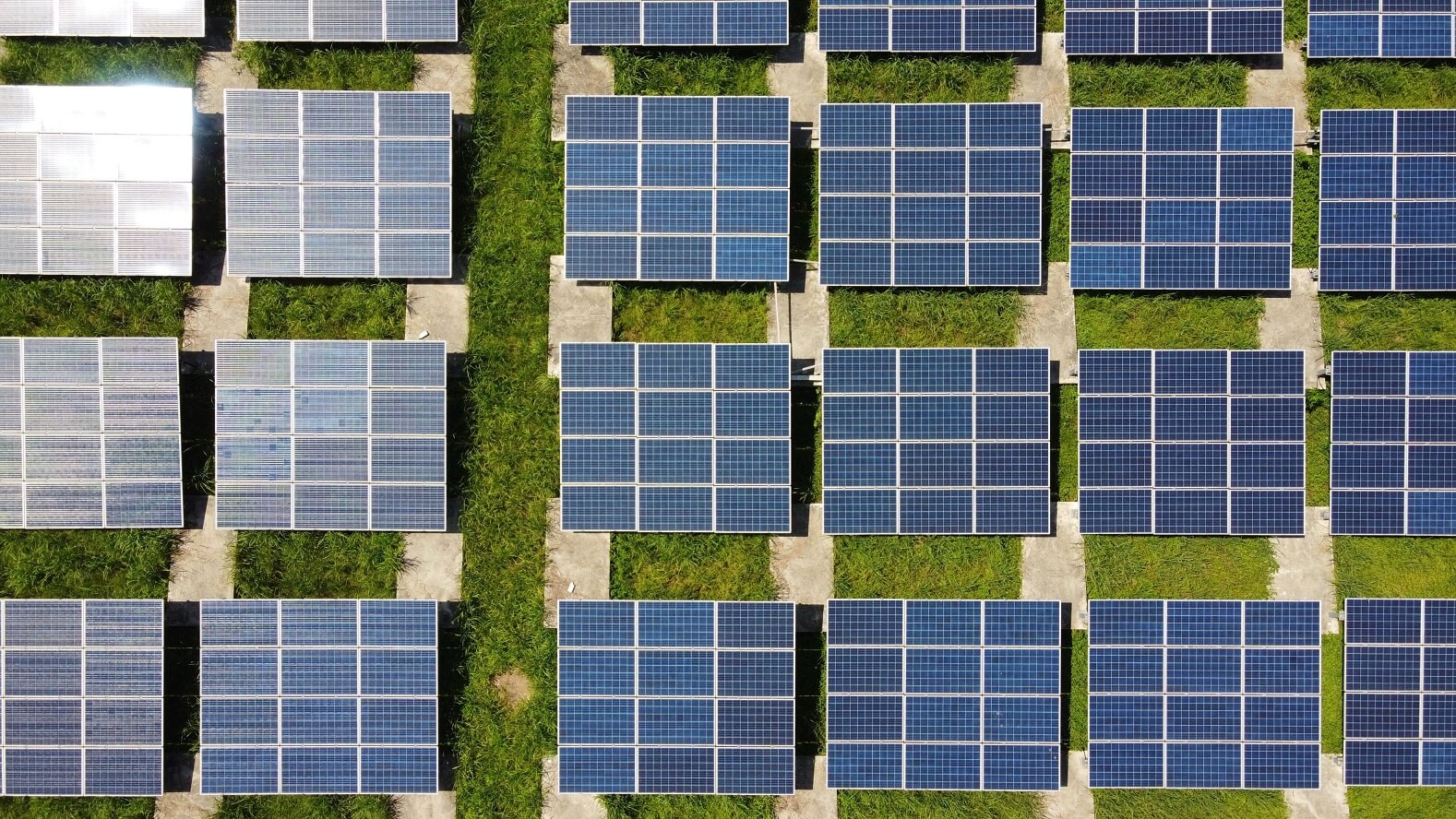
Competitive Edge of WMS and OMS in the E-commerce Market
The fierce competition in the e-commerce market requires businesses to do more than offer desirable products and services. In the digital age, operational efficiency is key to staying ahead. Integrating warehouse and order management systems are crucial to achieve this goal.
While warehouse and order management systems hold distinct functions, they are complementary and provide businesses with a competitive edge. Here are noteworthy advantages of implementing both strategies:
- Improved Inventory Management: Warehouse management systems (WMS) help accurately track stock levels and reduce overstocking or understocking situations. This precise inventory management leads to cost savings and ensures products are readily available for customer orders.
- Streamlined Order Processing: Order management systems (OMS) enable faster and more accurate order processing. Businesses can reduce errors, save time, and enhance customer experience by automating various steps in the order fulfilment process.
- Enhanced Customer Satisfaction: Quick and accurate order fulfilment, a direct result of effective OMS and WMS, improves customer satisfaction. This feature is crucial in building customer loyalty and reputation in the competitive e-commerce space.
- Data-Driven Decision Making: Both systems generate valuable data that can be analysed for insights into customer behaviour, inventory trends, and operational efficiency. This information aids in making informed decisions that align with business goals and market demands.
- Reduced Operating Costs: As WMS and OMS streamline operations, you can reduce operational costs. For example, an integrated WMS and OMS can automate order fulfilment, leading to faster order processing and reduced labour costs. You'll undergo fewer processes and hire fewer people, resulting in significant monetary savings.
Best Features to Look for in a Warehouse Management System in 2024
There's a wide array of warehouse management systems available, but choosing the right one is critical. Selecting the one that aligns perfectly with your business needs can revolutionise your operations, boosting efficiency and productivity. Here are five key features to look for in a WMS:
- Customisation and Scalability: A good WMS should offer customisation options to suit your specific operational needs. It should also be scalable to grow with your business, accommodating increased inventory, additional warehouses, or expanding product lines without needing a complete system overhaul.
- Real-Time Data, KPI Reporting and Analytics: The system should provide real-time inventory levels, order status, and warehouse activity data. This feature enables proactive decision-making and helps identify and address issues promptly. Advanced analytics can also offer insights into trends and patterns, aiding in strategic planning. Several WMS solutions are now also capable of using AI to optimise decision-making and operational processes.
- Integration Capabilities: Look for a system that can seamlessly integrate with other software used in your business, such as ERP (Enterprise Resource Planning) systems, accounting software, and e-commerce platforms. Integration ensures a smooth data flow across different business functions, enhancing overall operational efficiency.
- User-Friendly Interface: A user-friendly interface is crucial for a WMS. It should be intuitive and easy to navigate, reducing the learning curve for your staff and minimising errors. This feature is essential for ensuring quick adoption and effective system utility.
- Mobile Compatibility: In a mobile-first world, having a WMS with mobile compatibility allows for flexibility in managing warehouse operations. It enables staff to access the system from anywhere in the warehouse using handheld devices, improving efficiency and responsiveness in operations.
Best Features to Look for in an Order Management System in 2024
Every order, regardless of its size, plays a crucial role in the success of an e-commerce business. In an era where customers prioritise hassle-free transactions, the significance of an efficient OMS cannot be overstated. Here are five essential features to consider when choosing an OMS:
- Order Tracking: Customers appreciate transparency. An OMS that provides real-time order tracking empowers customers with information about their purchase status, fostering trust and improving satisfaction.
- Automated Return Management: Efficient handling of returns is essential. Look for an OMS that automates the return process, making it easy for customers to return products and for you to manage and restock them efficiently.
- Cross-Channel Order Fulfilment: Today's customers shop across multiple channels. An OMS capable of managing orders from various channels (online, in-store, mobile) ensures a unified customer experience, which is crucial for brand consistency.
- Inventory Visibility Across Channels: An OMS should offer real-time visibility into inventory levels across all sales channels. This feature helps prevent overselling and stockouts, ensuring you can meet customer demand without overstocking.
- Customer Relationship Management (CRM) Integration: An OMS integrated with CRM systems enables a more personalised customer experience. It allows businesses to understand customer preferences and purchase history, tailor communications, and improve customer loyalty.
Compatibility of WMS with OMS
Integrating warehouse management systems (WMS) and order management systems (OMS) into one cohesive system advances operational efficiency. These two systems are inherently compatible, each complementing the other’s functionality.
The combined power of WMS and OMS in one system offers businesses a comprehensive view of their supply chain operations. This integration enables seamless communication between warehouse activities and order management, ensuring that inventory levels, order processing, and distribution are perfectly aligned. It eliminates redundancies and data discrepancies, leading to more accurate and efficient operations.
Integrating WMS and OMS also provides greater agility in responding to market demands and customer needs. Such integration is a strategic move towards optimising logistics and elevating the overall effectiveness of supply chain management.
Optimal business operations with trace.
Choose trace. as your reliable team for WMS, OMS and more. We work closely with you to identify your unique needs and implement the right solutions. We can assist you to understand key gaps and opportunities, define your functional requirements, go to market and select a vendor as well as implement the solution.
With our advanced tools and dedicated support services, we're committed to unlocking your business's full potential. Partner with trace. and together, we'll transform your operational efficiency. Call us at +61 401 682 620 for enquiries and price quotes.