Warehouse Design: A Blueprint for Efficient Order Fulfilment
The efficiency of warehouse operations is not just about space—it's about maximizing its potential. In the competitive world of retail, where margins are thin and customer expectations are high, a strategic approach to warehousing can spell the difference between profit and loss. Let’s deep dive into how optimal warehouse configurations, advanced technology, and streamlined processes can revolutionize your supply chain.
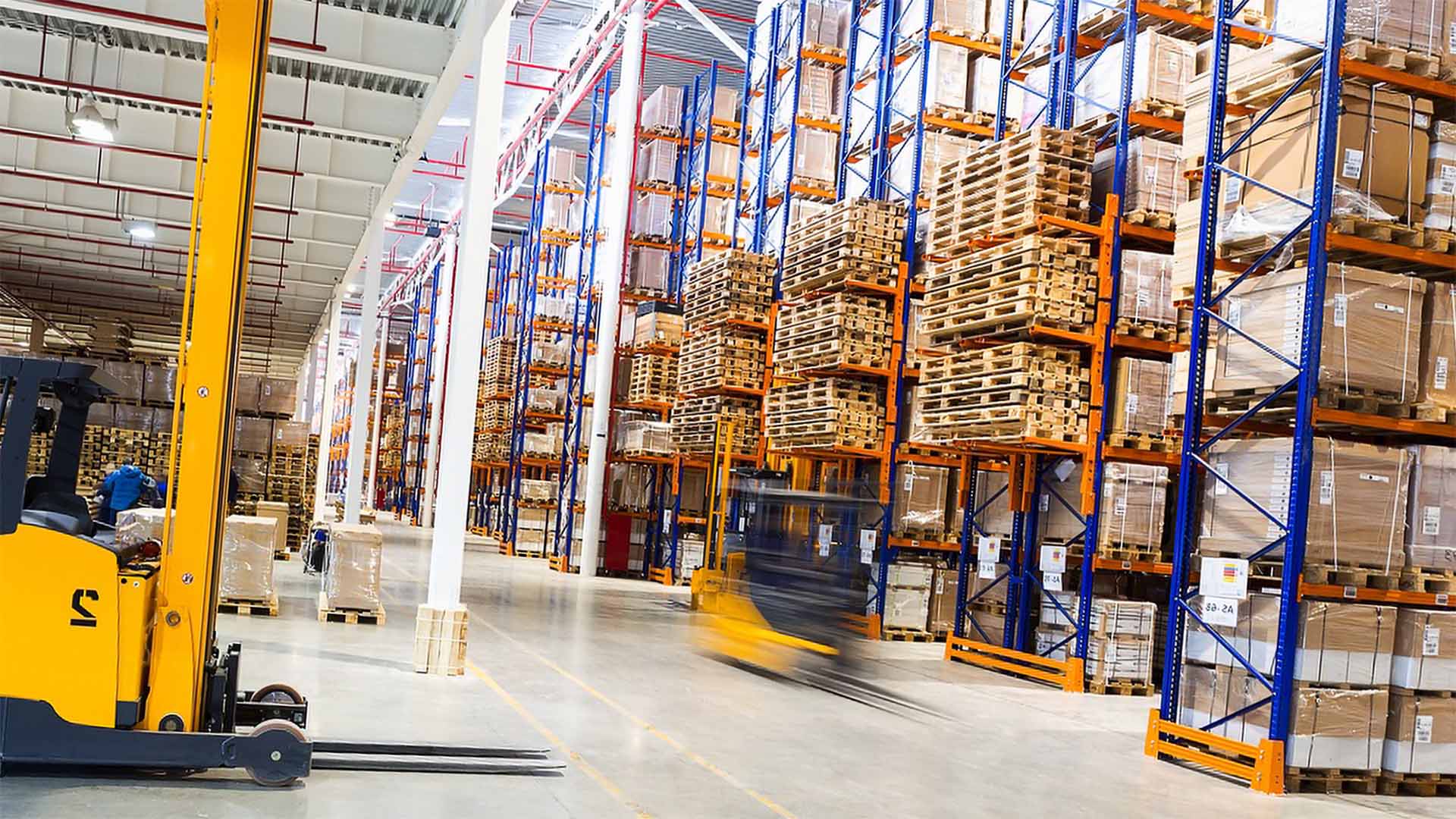
Demystifying Warehouse Configurations
The foundation of efficient warehousing lies in its configuration. Here's a deeper look at how various configurations suit different needs:
- Traditional Warehouses: These are spacious areas designed for long-term storage. Given their setup, they often incorporate large shelving units and extended aisle spaces, making them ideal for retailers with an expansive range of SKUs and stable demand.
- Cross-docking: Designed like a relay race, items come in on one side and leave almost immediately from the other. Cross-docking facilities often have multiple loading and unloading docks and minimal storage areas. It's ideal for perishable goods or promotional items that need quick shipping.
- Multi-tier Warehouses: These facilities maximize vertical space. They incorporate mezzanines, multi-level racking, and often utilize elevators or conveyance systems to move goods across levels. They're perfect for urban settings where land is expensive.
- Pop-up Distribution Centers: Essentially, these are makeshift warehouses, set up in strategic locations during peak demand seasons. Often, these might be tents, rented spaces, or even unused urban locales, outfitted temporarily for storage and dispatch.
Technology & Automation for Optimal Efficiency
Warehouses of today are becoming more tech-savvy. Let's delve into the tech tools that are making waves:
- Warehouse Management Systems (WMS): This is no ordinary software. Modern WMS integrates AI to predict demand, uses real-time data to monitor inventory levels, and can even integrate with e-commerce platforms to synchronize order data.
- Automated Storage & Retrieval Systems (AS/RS): Think of it as a giant vending machine. Items are stored in precise locations and are retrieved by automated machines that navigate the warehouse, increasing speed and reducing errors.
- Robotics: Beyond traditional conveyor belts, warehouses now deploy robots for a plethora of tasks. From bots that can navigate aisles picking items to robotic arms that pack boxes, automation is reducing dependency on manual labor.
- Internet of Things (IoT): With sensors on racks, pallets, and even individual products, real-time tracking has never been easier. It helps in inventory management, ensuring goods are stored and moved optimally.
- Drones: Imagine doing a full warehouse inventory in hours instead of days. Drones equipped with cameras and sensors can fly through aisles, scanning barcodes, and checking inventory levels.
Process Methodologies: The Backbone of a Streamlined Warehouse
Technology alone isn’t the answer; the processes driving them are just as vital:
- Lean Warehousing: Rooted in the principles of minimizing waste, lean warehousing emphasizes optimal space usage, streamlined pick-pack processes, and constant process evaluation.
- Just in Time (JIT): By partnering closely with suppliers, warehouses can adopt JIT to receive stock precisely when needed, minimizing storage costs and ensuring product freshness.
- ABC Analysis: Through this, inventory is classified based on its value and sales frequency. 'A' items are high-value products sold frequently, requiring prime storage locations, while 'C' items are low-value, slow-moving products that can be stored away from primary areas.
- Batch Picking: Rather than walking the entire warehouse for a single order, pickers gather items for multiple orders in one go. This reduces transit time and improves efficiency.
- Zone Picking: This requires dividing the warehouse into zones and assigning pickers to specific areas, ensuring they become experts in their respective zones, speeding up the picking process.
To thrive in today's retail world, rethinking warehouse strategy is paramount. By tailoring warehouse design, embracing tech innovations, and honing processes, retailers can ensure their supply chain becomes a strength, not a bottleneck. Because in today's fast-paced retail environment, it's not just about selling a product, but delivering an experience.