Back-of-House (BOH) logistics might not capture the same attention as front-line healthcare services, yet its role in hospitals and healthcare facilities is critical. Properly designed and efficiently operated back-of-house logistics are fundamental to ensuring seamless patient care, maintaining clinical outcomes, and supporting safe and efficient hospital operations. This article explores the key areas of BOH logistics optimisation, and how Trace Consultants can help Australian healthcare providers achieve their desired outcomes.
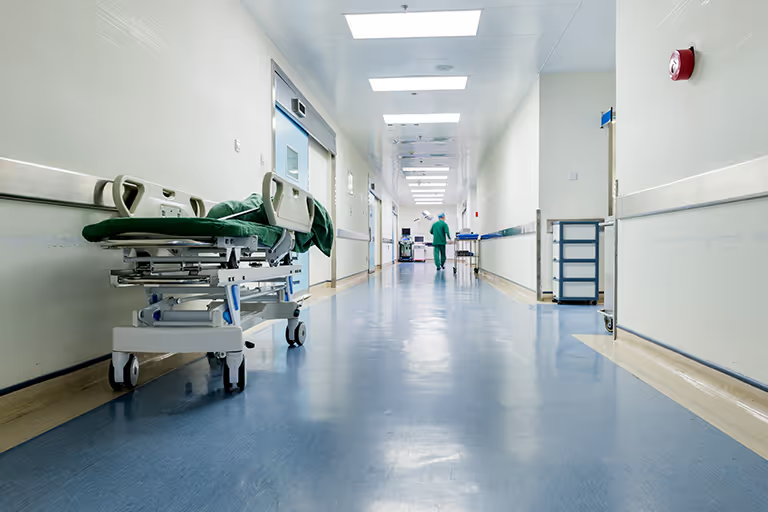
The Importance of Back-of-House Logistics
Back-of-house (BOH) logistics encompasses the vital infrastructure and processes that occur behind the scenes in hospitals, significantly impacting patient care and operational effectiveness. BOH logistics covers:
- Loading Dock Design
- Central Stores Layout
- Linen Services
- Production Kitchens
- Waste Management
- Dock-to-Ward Logistics
A poorly optimised BOH can negatively impact operational efficiency, patient safety, and staff satisfaction. Conversely, effective BOH logistics enhances clinical effectiveness, reduces operational risks, and ensures hospitals can meet increasing patient demands seamlessly.
Loading Dock Design
The loading dock acts as the nerve centre for hospital deliveries, from medical supplies to food and linen. Effective loading dock design ensures:
- Reduced congestion and improved traffic flow
- Efficient handling of deliveries
- Enhanced security and reduced risks of contamination
Trace Consultants collaborates with architects and facility planners to design loading docks that facilitate efficient movement and accurate receipt of supplies, optimising logistics flows and minimising disruption.
Central Stores Layout and Capacity Planning
Central stores are critical to inventory management, ensuring the right supplies are always available. Effective layout design and capacity planning ensure easy access, efficient storage, and minimal stock-outs. Trace Consultants assist by analysing inventory data, forecasting requirements, and optimising storage designs, resulting in reduced waste, lower inventory holding costs, and improved service levels.
Linen Services and Operating Models
Hospitals depend on efficient linen services to maintain hygiene standards and patient comfort. Operational inefficiencies can cause significant delays or shortages, negatively impacting patient care and satisfaction. Trace Consultants work with hospitals to evaluate existing linen service models, recommending improvements such as in-house versus outsourced services, optimised inventory management, and automated replenishment systems.
Production Kitchens and Waste Management
Efficient kitchen operations directly impact patient satisfaction and nutritional outcomes. Trace Consultants review kitchen layouts, workflows, and technology solutions, recommending improvements to streamline production, manage food safety effectively, and reduce waste. Sustainable waste management practices not only minimise environmental impact but also reduce operational costs through improved recycling, waste segregation, and disposal practices.
Dock-to-Ward Optimisation
The journey from dock to ward is pivotal in maintaining the quality and timeliness of patient care. Trace Consultants help optimise internal transportation routes, schedule deliveries efficiently, and implement technology-driven solutions like real-time tracking to enhance responsiveness and reduce waste. This results in less downtime, improved inventory accuracy, and reduced operational costs.
Infrastructure and Operating Model Alignment
Effective BOH logistics require alignment between infrastructure design, technology, and operational models. Trace Consultants collaborate closely with architects, project managers, and clinical teams to develop comprehensive functional briefs that consider future growth, technology integration, and changing healthcare service models. This ensures that new facility designs are robust, flexible, and responsive to future demands.
Dock-to-Ward Optimisation
Efficient dock-to-ward operations rely on carefully planned supply routes, clear scheduling protocols, and technology integrations to track inventory and minimise delays. Trace Consultants utilise advanced analytics and process improvement methodologies to identify bottlenecks, streamline workflows, and implement effective logistics solutions tailored to each facility's unique needs.
How Trace Consultants Can Help
Trace Consultants specialise in optimising healthcare supply chains and logistics through deep expertise in infrastructure design, technology integration, and operational excellence. By partnering with architects, project managers, and healthcare providers, Trace ensures that BOH logistics are strategically integrated into hospital facility designs, helping clients deliver superior patient care, maintain compliance, and achieve cost efficiencies. From creating detailed functional briefs to supporting implementation, Trace Consultants are committed to ensuring your BOH logistics deliver sustainable, long-term benefits.
Optimising back-of-house logistics is vital for enhancing patient care, clinical outcomes, and operational efficiency in hospitals. Strategic considerations around loading dock design, central store layouts, linen services, production kitchens, waste management, and dock-to-ward processes significantly influence hospital performance. Trace Consultants offer expertise to ensure your hospital's back-of-house operations support clinical excellence and operational efficiency.
Are you ready to transform your hospital's back-of-house logistics to improve patient care and operational efficiency? Contact Trace Consultants today.