In the rapidly evolving landscape of supply chain management, low-code platforms like Microsoft Power Apps and Mendix empower companies to swiftly develop custom applications that integrate various data sources and device inputs (think Internet-of-Things (IoT) devices) without the need for extensive coding expertise. This democratisation of app development enables organisations to build solutions that connect several different services and inputs, allowing them to monitor supply chains in real-time and proactively address issues, significantly improving operational efficiency.
How Low-Code Platforms Assist with Solution Development
Low-code development platforms simplify the process of building applications by providing a graphical user interface and pre-built templates. Microsoft Power Apps, for instance, allows users to drag and drop components to create. Benefits for companies include:
1. Simplified Development Process
Users can create custom applications quickly, reducing the time and cost associated with traditional software development. This agility is crucial for supply chain operations that require swift adjustments to changing conditions.
2. Seamless IoT Integration
Power Apps can connect to IoT hubs and devices, enabling the collection and analysis of sensor data, such as weights on a shelf, or RFID tag scans. This integration facilitates real-time monitoring of assets, environmental conditions, and other critical parameters in the supply chain.
3. Real-Time Data Visualisation
The platform allows for the creation of dashboards and reports that visualise data in real-time. Decision-makers can access insights instantly, enabling proactive responses to potential disruptions.
4. Scalability and Flexibility
As business needs evolve, applications built on Power Apps can be easily modified or scaled, ensuring long-term relevance and utility.
Examples of Low-Code in Supply Chain Management
Several companies have embraced low-code platforms to enhance their supply chain operations. Here are two relevant examples:
AntTail: Tackling Last-Mile Medication Delivery with Mendix Low-Code Platform
AntTail, a Netherlands-based company specialising in pharmaceutical supply chain solutions, has significantly enhanced the last-mile delivery of medications. Recognising the critical importance of temperature control in managing pharmaceuticals, AntTail developed a smart application using the Mendix low-code platform that integrates IoT sensors to monitor and ensure the integrity of medications during transit. By placing IoT sensors within medication packages, they continuously track temperature conditions throughout the delivery process. This real-time data ensures that any deviations from the required temperature range are immediately identified, allowing for prompt corrective action.
Utilising the flexibility of Mendix's low-code platform, AntTail rapidly developed an application that collects and analyses sensor data, providing actionable insights for all stakeholders—including manufacturers, distributors, and patients. This end-to-end visibility helps in tracking shipments, verifying product authenticity, and ensuring timely deliveries.
Outcome and opportunities.
AntTail's solution assists pharmaceutical companies in complying with stringent regulations regarding the handling and transportation of medications by offering detailed records of temperature data for compliance audits and quality assurance processes. By guaranteeing that medications are stored and transported under optimal conditions, AntTail enhances patient safety and trust, reducing the risk of compromised medications reaching end-users. Additionally, the proactive monitoring system minimises product waste caused by spoilage, leading to significant cost savings for pharmaceutical companies.
Ardent Mills: Enhancing Supply Chain Operations with Microsoft Power Apps
Ardent Mills, the leading flour-milling and ingredient company in the United States, leveraged Microsoft Power Apps to streamline their supply chain and operational processes. Facing challenges with data silos and manual workflows across numerous facilities, they sought a solution to enhance efficiency, data accessibility, and collaboration—without the extensive time and costs associated with traditional software development.
Custom apps for anyone, by anyone.
By utilising the low-code capabilities of Microsoft Power Apps, Ardent Mills empowered their employees—regardless of technical expertise—to develop over 20 custom applications. These apps automated and digitised various manual processes, including inventory management, equipment inspections, and quality control procedures. The swift development cycle meant the company could promptly address specific operational needs, significantly improving efficiency.
Integrating Power Apps with Microsoft Dataverse, Ardent Mills established a centralised data platform that ensured consistent and accurate information across the organisation. Coupled with Power BI, they gained advanced analytics and real-time insights into supply chain operations, facilitating better decision-making and forecasting. The custom applications also enhanced collaboration among teams spread across different locations. For example, an app known as “Cross Check” ensures equipment is calibrated consistently across sites to maintain the quality of flour produced. This app allows quality managers and lab technicians from different plants to enter data directly, and it's currently live across 35 plants. Used monthly by over 70 quality managers, lab technicians, and others, it facilitates approximately 170 checks each month.
Outcome and opportunities.
By automating manual tasks, Ardent Mills reduced operational costs and minimised errors associated with paper-based processes. The scalability of Power Apps allowed them to continuously evolve their applications as business needs changed, ensuring long-term value and adaptability. This approach not only streamlined their operations but also fostered a culture of innovation and collaboration within the company.
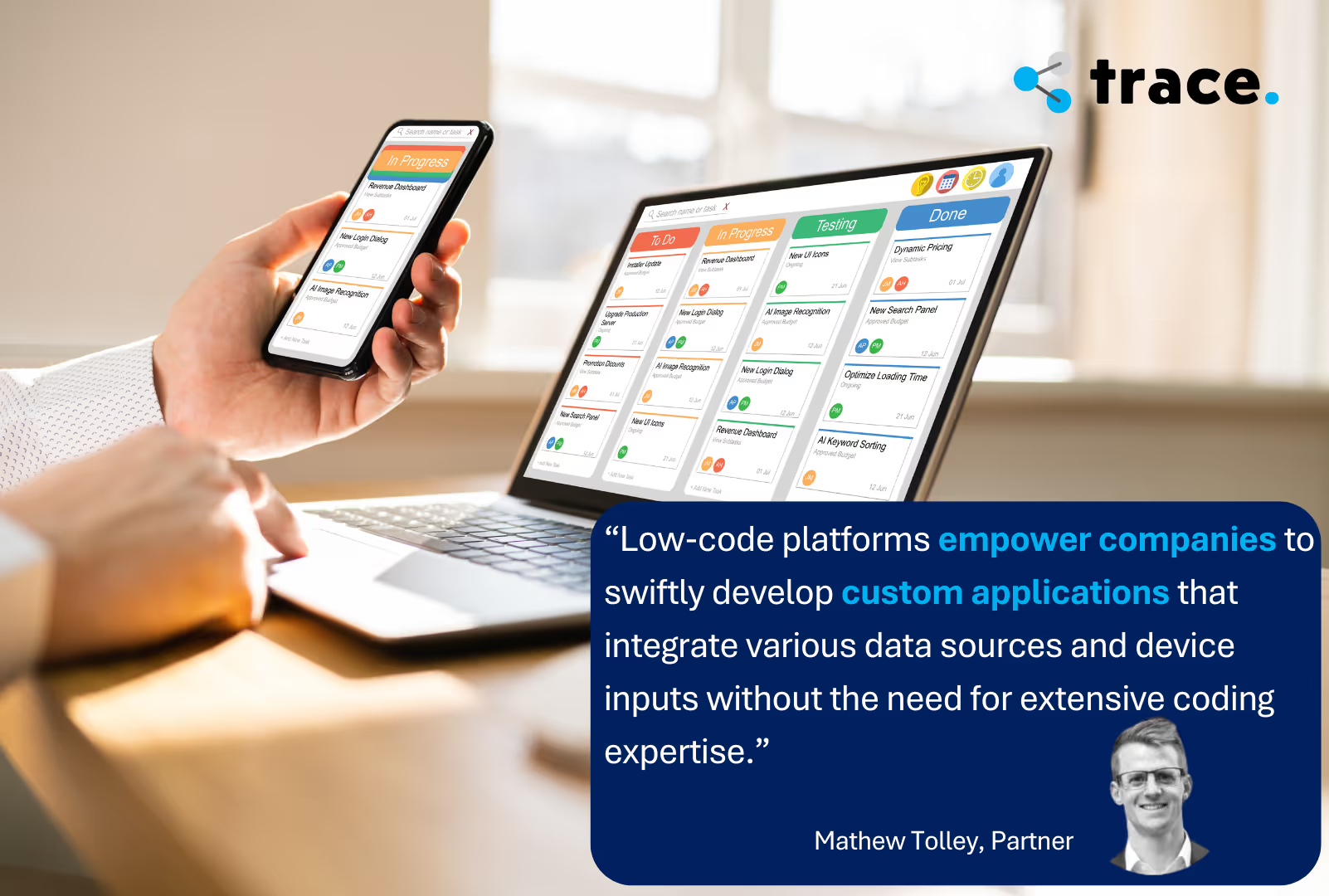
How Trace Consultants Can Assist Australian Companies
In light of the transformative benefits demonstrated by AntTail and Ardent Mills through the adoption of low-code platforms, Australian companies stand to gain significantly by embarking on a similar journey. Trace is uniquely positioned to guide businesses through the design, development, and deployment of tailored low-code solutions that enhance supply chain management. Here's how we can assist:
1. Strategic Assessment and Road mapping
To help your business maximise the benefits of low-code applications, we start by conducting a thorough supply chain analysis. Our team performs a comprehensive assessment of your current supply chain processes to identify areas where integrating low-code solutions can deliver the most value. By pinpointing these key areas, we can recommend targeted solutions that enhance efficiency and visibility across your entire supply chain.
Following this, we assist in developing a tailored technology strategy. We work with you to formulate a strategic roadmap that aligns technological solutions with your specific supply chain objectives, ensuring a focused approach to digital transformation. This roadmap guides the implementation of low-code applications in a way that supports your goals, optimises processes, and facilitates a smooth transition to more advanced supply chain management.
2. Design and Development of Custom Low-Code Applications
Leveraging our expertise in low-code platforms like Microsoft Power Apps, our team designs custom applications tailored to address your specific operational challenges. Whether it's demand planning, inventory management, or real-time asset monitoring, we create solutions that streamline processes and enhance efficiency. By focusing on your unique needs, we ensure that the applications we develop not only solve immediate issues but also contribute to long-term operational success.
3. Seamless Integration and Deployment
We ensure that new applications integrate seamlessly with your existing systems such as ERP, CRM, and legacy supply chain applications, providing a unified platform for all supply chain activities. Our integration process minimises disruptions and ensures that all components of your supply chain work harmoniously together. Additionally, we provide comprehensive training for your staff to maximise the adoption and effective use of new applications. By fostering a culture of innovation within your organisation, we help your team embrace new technologies confidently and efficiently.
Benefits of Partnering with Trace Consultants
1. Accelerated Implementation
Our expertise significantly reduces the time from concept to deployment. By streamlining the development process and leveraging the efficiencies of low-code platforms, we enable you to realise benefits much sooner than traditional development methods would allow. This rapid turnaround not only accelerates your return on investment but also allows your business to respond quickly to market changes and opportunities.
2. Cost-Effective Solutions
By utilising low-code platforms, we minimise development costs while delivering high-quality, customised applications tailored to your specific needs. The reduced need for extensive coding and shorter development cycles mean lower expenditure without compromising on functionality or quality.
3. Empowered Workforce
Through comprehensive training and the implementation of user-friendly applications, we empower your employees to actively contribute to process improvements and innovation. By involving your team in the development and utilisation of these tools, we foster a culture of continuous improvement and engagement. The low-code ecosystem is a great way to engage super users in developing and improving tactical solutions, while adhering to IT governance policies on architecture, security, and access.
Conclusion
The success stories of AntTail and Ardent Mills illustrate the profound impact that low-code platforms can have on supply chain management. By partnering with Trace, Australian companies can unlock similar benefits—enhancing operational efficiency, engaging users in solution design, and improving processes and technology in a cost effective way.
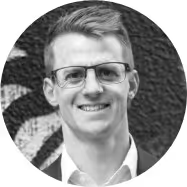
Mathew Tolley
Partner