Warehousing has undergone a significant evolution, particularly with the advent of e-commerce. Traditional warehousing primarily focused on storing products until they were ready for physical retail. E-commerce warehousing is dynamic and fast-paced. It prioritises efficient inventory management, quick product turnover, and speedy deliveries.
The e-commerce shift transformed warehouses into crucial supply chain nodes, adapting to the unique demands of online consumers. Adapting to this new normal in warehousing can be a slow and gradual process. However, with the guidance of experts like trace., you can accelerate the transition, adopting best practices that align with your e-commerce objectives.
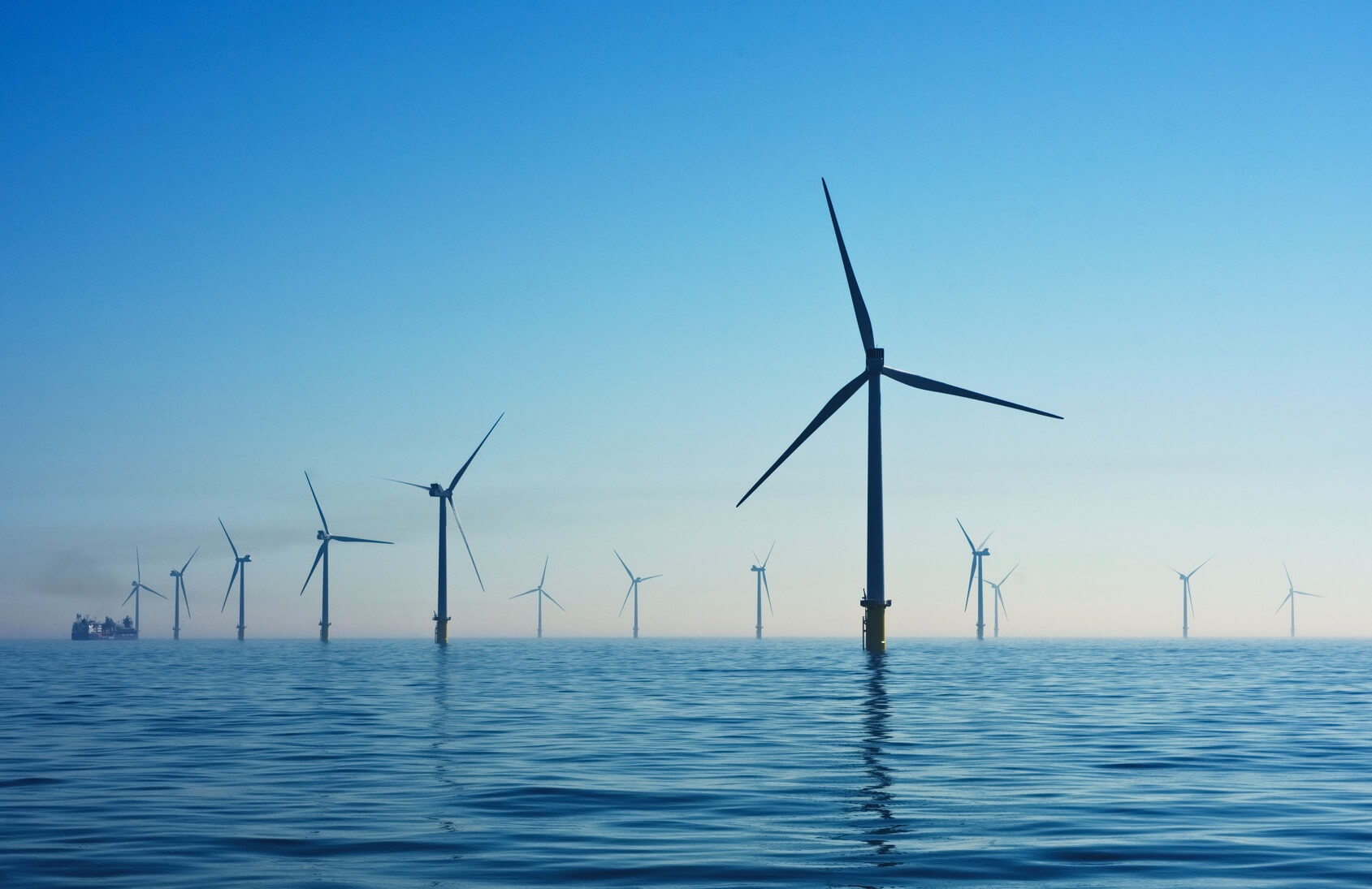
Inventory and Warehouse Management in the e-Commerce Market
The digitisation of commerce has significantly raised the bar for warehouse management. The rapid pace and heavy volume of online transactions require a more sophisticated approach to managing stock levels and warehouse operations. Modern solutions involve leveraging advanced technologies to automate processes, accurately track inventory in real-time, and optimise warehouse space for efficient order fulfilment.
As e-commerce continues to grow, adapting these digital advancements becomes essential for businesses to remain responsive to market demands. trace. can introduce you to digital solutions that best fit your business needs. Our warehousing management expertise will give you a competitive advantage over others.
How do e-commerce sites manage their inventory?
A reliable warehouse system ensures an e-commerce site's accurate stock level tracking while preventing stockouts. For optimal management, some e-commerce sites adopt real-time tracking to monitor stock levels continuously. Utilising automated reordering systems can avoid shortages of inventory. Regular analysis of sales data helps in forecasting demand accurately.
Integrating inventory management with other business systems, like CRM and accounting software, provides a holistic view of operations. Adopting these strategies ensures a well-managed inventory, which is crucial for the success of any e-commerce venture.
How do e-commerce sites manage their warehouses?
There are many ways e-commerce sites succeed with warehouse management. Our top recommendation is to use a warehouse management system (WMS) software to enjoy the following advantages:
- Accurate stock monitoring
- Prevention of stockouts
- Reduction of production waste
- Avoid inventory shortages
- Accurate forecasting of demands
- Integration with other tools, like ERP systems, CRM and other software, for a more holistic operation
For more options, coordinate with trace. We will analyse your needs and propose solutions that can deliver optimal results.
Different Types of e-Commerce Warehouses
E-commerce has revolutionised how businesses approach logistics and distribution, leading to various types of warehouses, each tailored to different aspects of online retail.
These e-commerce warehouses offer unique advantages. Choose which ones that align with your needs:
- 3PL Warehouses: Third-party logistics (3PL) warehouses handle inventory management, order fulfilment, and shipping on behalf of the e-commerce business. They are ideal for scaling operations without investing in their own warehouse infrastructure. 3PL providers offer the advantage of logistics expertise and can often negotiate better shipping rates due to their volume.
- Traditional Warehouses: These facilities are often larger and can be configured to accommodate a wide range of products. They provide businesses with complete control over their inventory and logistics operations, but this comes with the responsibility of managing the entire supply chain process.
- Fulfilment Centres: Fulfilment centres are specialised warehouses designed to handle the order fulfilment process efficiently. They focus on processing orders quickly - from picking and packing to shipping. These centres are often strategically located to minimise shipping times and costs, making them essential for e-commerce businesses that promise rapid delivery times.
- Dark Stores: Dark stores are retail distribution centres that cater exclusively to online shopping. They resemble retail stores but are closed to customers, functioning solely as a hub for picking and packing online orders. Dark stores enable faster fulfilment of online orders, particularly for grocery and fast-moving consumer goods.
- Automated Facilities: Automated facilities represent the cutting edge in warehouse technology. They use automation and robotics for efficient inventory management and order processing. These facilities are highly efficient, reduce manual errors and labour costs, and are ideal for e-commerce businesses with high order volumes.
- Store Fulfilment: Store fulfilment involves using retail stores as mini distribution centres for online orders. Retailers use their existing stores to fulfil online orders through in-store pickup options (click and collect) or by shipping directly from store to customer. This approach leverages the retail footprint to offer faster delivery and reduce shipping costs.
Recommended inventory and warehouse management strategies
In the dynamic world of e-commerce, effective inventory and warehouse management are crucial to staying competitive and meeting customer expectations. Here are six essential strategies to optimise these critical areas:
- Real-Time Inventory Tracking: Implementing real-time inventory tracking systems is crucial. It provides up-to-date information on stock levels, enabling quick response to changes in demand. This strategy helps prevent stockouts and overstocking, ensuring that inventory is always aligned with current sales trends.
- Automated Reordering Systems: To maintain optimal stock levels, automated reordering systems can be a game-changer. These systems use predefined criteria to automatically place orders when stock levels drop below a certain point, ensuring you never run out of popular products.
- Efficient Space Utilisation: Maximising warehouse space efficiency is vital. It involves organising products based on size, frequency of access, and sales velocity. Efficient space utilisation saves costs and streamlines picking and packing processes.
- Advanced Picking Methods: Adopting advanced picking methods like batch picking, zone picking, or wave picking can significantly increase order fulfilment efficiency. These methods reduce the time and effort spent retrieving products from the warehouse, speeding up the delivery process.
- Integrating Warehouse Management Systems (WMS): A robust WMS can transform warehouse operations. These systems help manage and optimise the placement and movement of goods within the warehouse, improving overall efficiency, accuracy, and speed of order processing.
- Seasonal Demand Planning: E-commerce businesses often experience seasonal fluctuations. Planning for these variations in demand is essential. It involves analysing sales data to anticipate increases in demand and adjusting inventory and warehouse operations accordingly to handle the surge without hiccups.
With the right combination of these practices, e-commerce businesses can achieve a streamlined, responsive, and cost-effective operation.
Choosing better warehousing solutions
Warehousing solutions are now more accessible than ever, but selecting one that aligns with your business needs can be challenging. It's important to trust professionals in this decision-making process. Expert guidance can help you navigate the myriad of options and choose the right warehouse type and technology solution that perfectly suits your business requirements. We can assist you to understand key gaps and opportunities, define your functional requirements, go to market and select a vendor as well as implement the solution.
trace. has in-depth knowledge and experience to guide you in resolving warehousing needs effectively. We simplify supply chain management for you, breaking down complex processes into manageable steps. Whether you're just starting or looking to refine your existing operations, our consultancy services can be tailored to meet your needs.
There's no need to navigate the complexities of e-commerce warehousing by yourself. Seek our expert guidance today.