The Olympic Games, a global spectacle of athletic prowess and unity, stand as one of the most logistically complex events in the world. The successful execution of the Olympics relies on an intricate web of supply chains, from the athletes' villages to transport, events, food and beverage (F&B), and hospitality. As Paris hosts the 2024 Summer Olympics and Brisbane gears up for 2032, understanding and mastering these supply chains is paramount to delivering a memorable and smoothly run event.
Trace Consultants, an Australian boutique supply chain advisory firm, is well-positioned to offer its expertise to ensure the seamless operation of these multifaceted supply chains.
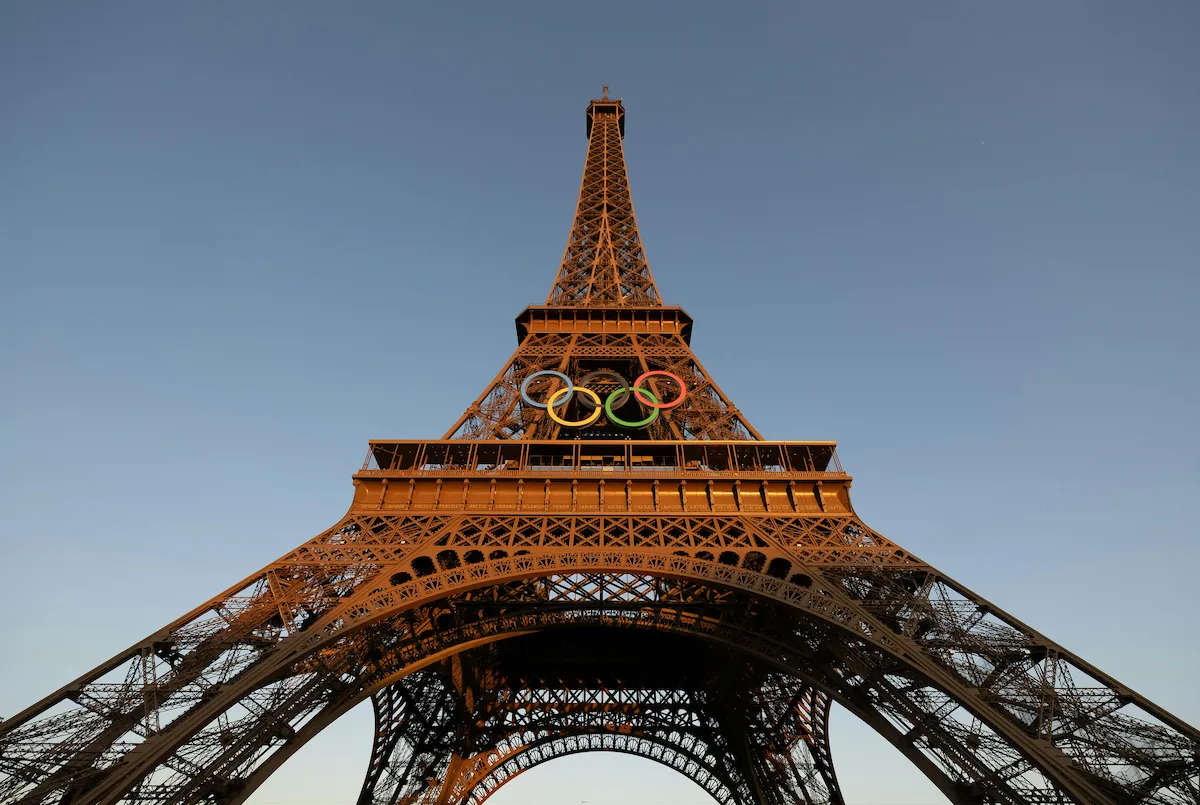
Athletes' Villages: The Heart of the Games
The athletes' village is the nucleus of the Olympic Games, housing thousands of athletes and support staff from around the world. The supply chain for these villages involves several critical components:
- Construction and Infrastructure: Building the village involves sourcing materials, managing construction timelines, and ensuring sustainability. This requires coordination with local suppliers, construction companies, and sustainability experts to meet deadlines and adhere to environmental standards.
- Accommodation and Amenities: Once built, the villages must be outfitted with furniture, bedding, appliances, and recreational facilities. Suppliers must deliver high-quality products that meet the needs of diverse athletes, from dietary preferences to cultural considerations.
- Security and Safety: Ensuring the safety and security of the athletes is paramount. This involves integrating advanced security systems, emergency response protocols, and healthcare services.
- Maintenance and Operations: Throughout the Games, the village must operate smoothly, requiring continuous supply of essentials such as food, medical supplies, and maintenance services.
Transport: The Artery of the Olympics
Transportation is the lifeblood of the Olympics, facilitating the movement of athletes, officials, spectators, and goods. The transport supply chain encompasses:
- Public Transport Infrastructure: Host cities must upgrade and expand their public transport networks to handle the influx of visitors. This involves synchronising with local transit authorities, managing construction projects, and ensuring accessibility.
- Fleet Management: A fleet of buses, cars, and specialised vehicles is required to transport athletes and officials between venues. This involves coordinating with vehicle manufacturers, managing fuel supplies, and ensuring timely maintenance.
- Traffic Management: Efficient traffic management systems are critical to avoid congestion and ensure smooth transport. This includes real-time monitoring, traffic control systems, and clear communication with the public.
- Sustainability Initiatives: Modern Olympics prioritise sustainability, requiring the integration of electric vehicles, bike-sharing programs, and carbon offset initiatives in the transport plan.
Event Logistics: The Backbone of the Games
Event logistics is the backbone of the Olympic Games, involving the coordination of various activities to ensure that events run smoothly:
- Venue Management: Each sporting venue requires meticulous planning, from construction to daily operations. This includes managing supply chains for sports equipment, seating arrangements, and broadcasting facilities.
- Scheduling and Coordination: Coordinating the schedule of events, athlete arrivals, and practice sessions requires advanced logistics planning to avoid conflicts and ensure punctuality.
- Technology and Communication: Reliable technology and communication networks are essential for managing events, providing real-time updates, and ensuring smooth operations.
- Volunteer Management: Thousands of volunteers are critical to the success of the Olympics. This involves recruitment, training, and coordination to ensure they are well-prepared to assist in various capacities.
Food and Beverage (F&B): Fueling the Games
The F&B supply chain is crucial for the well-being of athletes, officials, and spectators:
- Catering Services: Providing nutritious and diverse meals for athletes requires coordination with nutritionists, chefs, and suppliers to meet dietary requirements and cultural preferences.
- Vendor Management: Managing a vast network of food vendors to serve spectators involves ensuring quality, safety, and timely delivery of food and beverages.
- Sustainability Practices: Modern Olympic Games emphasise sustainability, necessitating the use of eco-friendly packaging, waste reduction strategies, and sourcing from local and sustainable suppliers.
- Health and Safety Standards: Ensuring the highest standards of food safety and hygiene is critical to prevent any health issues during the Games.
Hospitality: Enhancing the Olympic Experience
Hospitality plays a significant role in shaping the experience of athletes, officials, and spectators:
- Accommodation Management: Beyond the athletes' village, providing accommodation for officials, media, and spectators involves partnering with hotels and rental services to ensure availability and quality.
- Event Hospitality: VIP guests and sponsors require special hospitality arrangements, including exclusive lounges, fine dining, and personalised services.
- Customer Service: Ensuring a positive experience for all attendees requires exceptional customer service, from ticketing to on-ground assistance.
- Cultural Integration: Highlighting the host city's culture through hospitality services enriches the overall Olympic experience.
Production Kitchens: Ensuring Culinary Excellence
Production kitchens are crucial for delivering high-quality meals across various Olympic venues:
- Centralised Cooking: Establishing central production kitchens allows for large-scale meal preparation, ensuring consistency and quality.
- Menu Planning: Collaboration with nutritionists and chefs to develop menus that cater to diverse dietary needs and preferences.
- Logistics Coordination: Efficient distribution of prepared meals to various venues, ensuring timely delivery and optimal freshness.
Waste & Sustainability: Leaving a Positive Legacy
Sustainability is a core focus for modern Olympics, necessitating robust waste management and sustainability practices:
- Waste Reduction: Implementing strategies to minimise waste, such as using recyclable materials and reducing single-use plastics.
- Recycling Programs: Establishing comprehensive recycling programs to manage waste effectively and promote environmental responsibility.
- Sustainable Sourcing: Prioritising suppliers and products that adhere to sustainable practices, reducing the overall environmental footprint of the Games.
Linen Services: Managing Essential Supplies
Linen services are a critical component of the hospitality and athlete accommodation sectors:
- Supply Chain Coordination: Ensuring a continuous supply of clean linens, towels, and uniforms across all venues.
- Quality Control: Maintaining high standards of cleanliness and hygiene to ensure the comfort and well-being of athletes and guests.
- Sustainable Practices: Implementing eco-friendly laundering processes to minimise water and energy consumption.
Procurement Activities: Ensuring Efficient Supply Chains
Effective procurement is vital for managing the vast array of goods and services required for the Olympics:
- Supplier Selection: Identifying and partnering with reliable suppliers that can meet the high standards and timelines of the Games.
- Contract Management: Negotiating and managing contracts to ensure compliance and value for money.
- Cost Management: Implementing strategies to control costs while maintaining quality and sustainability.
Distribution Centers and Warehousing: Backbone of Supply Chain
Distribution centers and warehousing are essential for managing the flow of goods:
- Centralised Warehousing: Establishing central warehouses to store and manage inventory, ensuring efficient distribution to various venues.
- Inventory Management: Using advanced inventory management systems to track stock levels, forecast demand, and prevent shortages.
- Logistics Coordination: Coordinating transportation and delivery schedules to ensure timely and efficient distribution.
The Key to a Successful Olympics: Integration and Coordination
The success of the Olympic Games hinges on the seamless integration and coordination of these diverse supply chains. Key strategies include:
- Advanced Planning and Forecasting: Accurate forecasting and meticulous planning are essential to anticipate demand, allocate resources, and prevent bottlenecks.
- Collaboration and Communication: Effective collaboration between various stakeholders, including government agencies, suppliers, and service providers, ensures smooth operations.
- Technology Integration: Leveraging technology for real-time monitoring, communication, and data analysis enhances decision-making and operational efficiency.
- Sustainability Initiatives: Integrating sustainability into every aspect of the supply chain minimises the environmental impact and aligns with modern values.
- Risk Management: Proactive risk management strategies, including contingency planning and crisis response, are critical to address unforeseen challenges.
Paris 2024 and Brisbane 2032: A Glimpse into the Future
As Paris prepares for the 2024 Summer Olympics and Brisbane looks ahead to 2032, these cities have unique opportunities to showcase their capabilities and innovations in supply chain management.
Paris 2024: Embracing Sustainability and Innovation
Paris 2024 is committed to delivering an environmentally sustainable and innovative Olympic Games. Key initiatives include:
- Eco-friendly Infrastructure: Paris aims to use existing venues and build new ones with sustainable materials and energy-efficient designs.
- Green Mobility: The city plans to enhance its public transport network and promote the use of electric and shared vehicles.
- Circular Economy Practices: Emphasising waste reduction, recycling, and the use of renewable resources in all aspects of the Games.
- Technology Integration: Leveraging advanced technologies for event management, security, and fan engagement.
Brisbane 2032: A Vision for Future-proof Games
Brisbane 2032 envisions a forward-thinking Olympic Games that prioritise community engagement and long-term benefits:
- Community-centric Planning: Engaging local communities in the planning process to ensure the Games leave a positive legacy.
- Innovative Infrastructure: Developing smart, sustainable infrastructure that serves the city long after the Games.
- Enhanced Connectivity: Investing in transport and communication networks to ensure seamless connectivity.
- Focus on Legacy: Prioritising projects that deliver lasting benefits to the city and its residents.
How Trace Consultants Can Help
Trace Consultants, an Australian boutique supply chain advisory firm, is uniquely positioned to support the successful delivery of the Olympic Games. With expertise in supply chain optimisation, project management, and sustainability, Trace Consultants can offer invaluable assistance in:
- Supply Chain Optimisation: Streamlining supply chains for efficiency, cost-effectiveness, and sustainability.
- Project Management: Ensuring timely and successful execution of projects, from construction to event logistics.
- Risk Management: Identifying and mitigating risks to ensure smooth operations across procurement, warehouse & transport operations.
- Sustainability Consulting: Integrating sustainable practices into every aspect of the supply chain.
- Technology Integration: Leveraging technology to enhance operational efficiency and decision-making.
By partnering with Trace Consultants, organisers of events such as Paris 2024 and Brisbane 2032 can ensure the delivery of an unforgettable Olympic Games that set new standards in sustainability, innovation, and community engagement.
The Olympic Games represent a pinnacle of global unity and athletic achievement, but they also present immense logistical challenges. From the athletes' villages to transport, events, F&B, hospitality, production kitchens, waste management, linen services, procurement activities, and distribution centers, every aspect of the supply chain must be meticulously planned and executed. As Paris 2024 and Brisbane 2032 approach, leveraging the expertise of supply chain specialists like Trace Consultants will be crucial to delivering successful and memorable Olympic Games. By embracing innovation, sustainability, and community engagement, these cities can set new benchmarks for future Olympic Games, ensuring a lasting legacy of positive impact.