Supply chains play a substantial role in the world's carbon emissions. The energy-intensive manufacturing, transportation, warehousing, and distribution processes escalate environmental pollution and global carbon footprints.
As the damages of climate change concerns intensify, businesses must opt for environmental stewardship. Decarbonisation emerges as a formidable strategy for fostering eco-conscious operations. Beyond its ethical implications, sustainability initiatives hold the potential to elevate businesses' operational efficiency and yield significant cost reductions.
When you partner with trace., you gain access to sustainable solutions tailored to your specific needs. Our team of experts specialises in optimising supply chain systems with minimal environmental impact. Consult with us to identify and efficiently implement eco-friendly practices that align seamlessly with your business objectives.
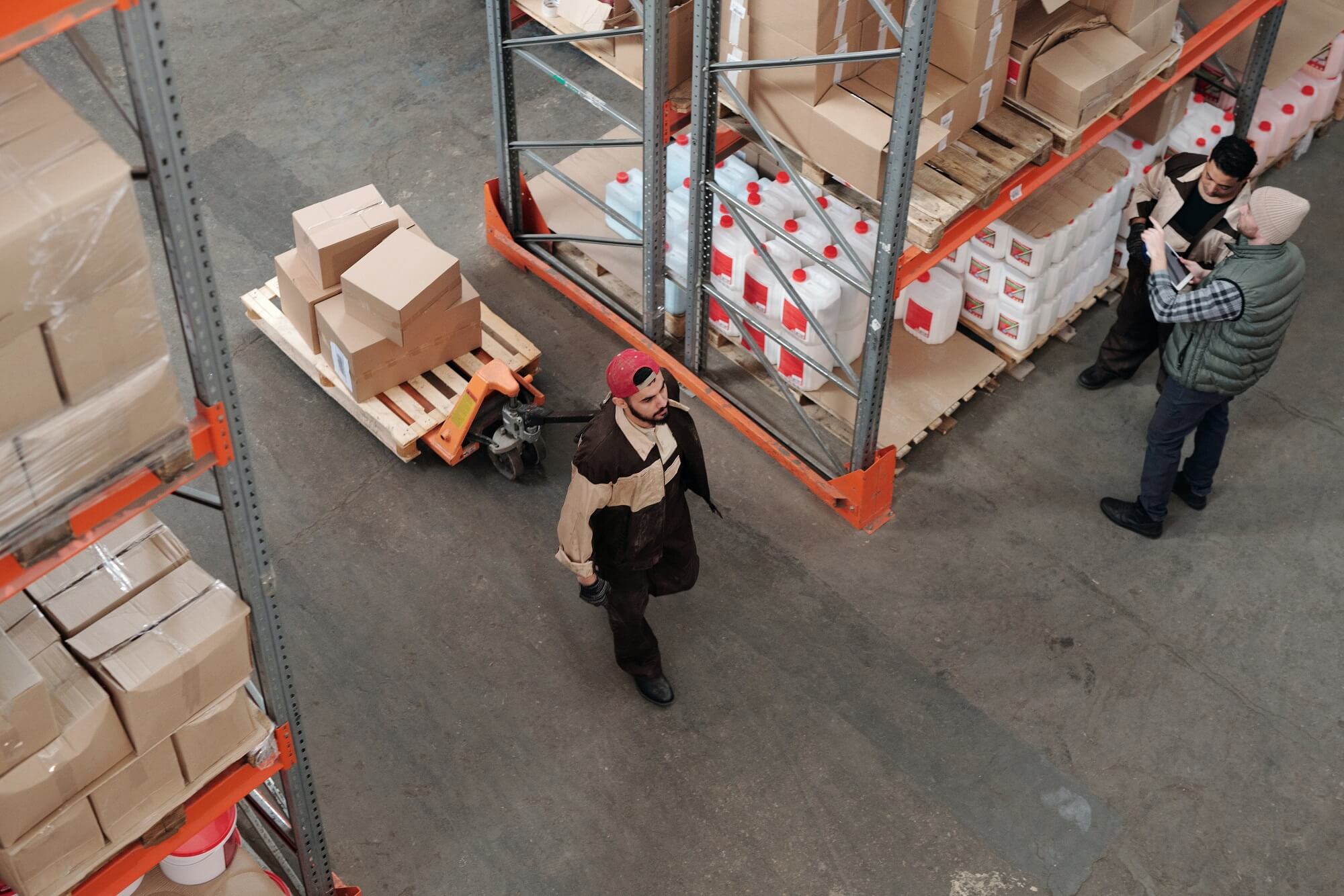
Understanding Decarbonisation
Decarbonisation signifies the reduction of carbon dioxide emissions, with a primary focus on curbing emissions originating from fossil fuel usage. Over time, spurred by heightened environmental awareness and technological advancements, decarbonisation has transitioned from a mere theoretical concept to a practical and imperative goal. Today, it stands as a widely adopted practice, driven by environmental concerns and the potential for significant long-term economic benefits.
Achieving decarbonisation is undeniably attainable, albeit it necessitates unwavering commitment from businesses. Companies must be prepared to institute substantial changes in their operational methodologies and invest in sustainable supply chain systems. As more companies embrace decarbonisation, this endeavour transcends individual actions, evolving into a collective global initiative dedicated to preserving our planet.
Decarbonisation Is Not a Lost Cause
Decarbonisation is a challenging yet achievable objective that demands concerted efforts from governments, businesses, and various sectors. Companies should actively participate in this collective endeavour, contributing to a sustainable future that benefits all. Collaboration across industries is essential to drive meaningful progress toward a decarbonised world.
Understanding Life Cycle Assessment (LCA)
Life Cycle Assessment (LCA) is a systematic analysis method used to evaluate the environmental impacts associated with all the stages of a product's life, from raw material extraction through materials processing, manufacture, distribution, use, repair and maintenance, and disposal or recycling. By assessing a product's life cycle, LCA analyses the comprehensive environmental impacts and identifies areas for improvement in product development and decision-making processes.
The stages of LCA are as follows:
- Goal and Scope Definition: This initial stage defines the LCA's purpose and the system boundaries. It outlines the product or process to be assessed and determines the level of detail required based on the intended use of the assessment.
- Inventory Analysis (Life Cycle Inventory, LCI): This stage involves data collection and calculation procedures to quantify relevant inputs and outputs of a product system. It tracks the flow of energy, materials, and emissions in each stage of the product life cycle.
- Impact Assessment (Life Cycle Impact Assessment, LCIA): In this phase, the environmental impacts of resource use and emissions identified in the LCI are evaluated. It involves associating inventory data with specific ecological impacts, such as global warming, ozone depletion, and water pollution.
- Interpretation: The final stage involves analysing the inventory analysis and impact assessment results to make informed decisions or recommendations. It assesses the reliability and significance of the results and identifies the areas with the most significant environmental impacts for improvement.
What is the significance of life cycle assessment (LCA) in supply chain decarbonisation?
LCA is crucial to supply chain decarbonisation because it thoroughly analyses the environmental impacts of products. It enables businesses to identify the stages in their supply chain that contribute most significantly to carbon emissions. This holistic view is essential for developing targeted strategies to reduce carbon footprints effectively.
Companies can make informed decisions through LCA to implement more sustainable practices across their supply chains. LCA becomes an indispensable tool for businesses committed to reducing their environmental impact and achieving decarbonisation goals.
Reasons to Pursue a Sustainable Supply Chain
With the growing impact of climate change and resource depletion, businesses are increasingly held accountable for their environmental footprint. Beyond fulfilling this crucial responsibility, adopting sustainable practices in supply chains also brings practical benefits to companies. Embracing sustainability is not just about doing good for the planet; it's also about strategic business advantages.
- Cost Reduction: Implementing sustainable practices prioritises the efficient use of resources. This initiative reduces waste and operational costs over time. For instance, using less energy and fewer materials in production lowers expenses, providing a significant economic benefit in addition to the environmental one.
- Risk Mitigation: By their nature, sustainable supply chains are typically more resilient. They reduce risks associated with environmental regulations, which are becoming increasingly stringent. Additionally, they mitigate the risks of resource scarcity and climate-related disruptions, ensuring a more stable and predictable supply chain environment.
- Improved Brand Reputation: Consumers are increasingly environmentally conscious in today's market. Companies that adopt sustainable practices often enjoy enhanced brand loyalty and a stronger market position. They appear responsible and forward-thinking, qualities that attract and retain customers who value sustainability.
- Innovation Opportunities: Sustainability challenges businesses to develop new, more efficient processes and products. Consequently, it reduces environmental impact while opening up new markets and opportunities for growth.
- Long-term Viability: Aligning supply chains with sustainable practices ensures better positioning for long-term success. Companies with sustainable supply chains are prepared to meet consumers' evolving demands.
Steps to Decarbonise Your Supply Chain
There is no one-size-fits-all approach to decarbonisation, and businesses have several options to tailor their strategies according to their specific needs and capabilities. Here are some ways companies can decarbonise their supply chain:
- Waste Reduction and Recycling: Minimising waste in supply chain operations and maximising recycling efforts can contribute significantly to decarbonisation. This initiative involves adopting practices that reduce material wastage in production and recycling materials wherever possible.
- Switching to Renewable Energy: One of the most impactful ways to decarbonise is by transitioning to renewable energy sources, such as solar or wind power, for manufacturing and warehousing operations. This strategy greatly reduces carbon emissions and leads to long-term operational efficiency.
- Demand Planning & Inventory Optimisation: Demand planning, forecasting, and inventory optimisation in Australia significantly contribute to reducing carbon emissions by curtailing waste. These strategies ensure accurate product quantity predictions, avoiding overproduction and excess inventory. This approach not only diminishes the need for energy-intensive warehousing but also lessens reliance on carbon-heavy expedited shipping. Consequently, these practices foster a more sustainable supply chain, efficiently utilising resources and thus cutting down on waste and its related carbon footprint.
- Optimising Transportation and Logistics: Revamping the transportation and logistics strategy can significantly cut emissions. It includes adopting more efficient route planning, using vehicles with lower emissions, and considering alternative modes of transport like rail or electric cars. Newer models often come with more environmentally friendly features than traditional road transport.
- Implementing Sustainable Procurement Practices: Businesses can opt for sustainable procurement by choosing suppliers who prioritise environmentally friendly practices. This approach includes sourcing renewable raw materials with a lower carbon footprint and working with suppliers committed to sustainability.
- Investing in Energy-Efficient Technology: Investing in technology that enhances energy efficiency in production processes and warehouse operations can significantly reduce carbon emissions. It includes upgrading to energy-efficient machinery and implementing automated systems optimising energy use.
- Carbon Offsetting and Insetting: While reducing emissions is the primary goal, some residual emissions can be offset through carbon offsetting programs. Companies can also invest in carbon insetting projects, which involve creating or investing in carbon reduction initiatives within their own supply chain or community.
trace. is here to assist you in designing and implementing sustainable supply chain strategies that best fit your business. Our team of experts will comprehensively assess your operations and implement systems tailored to simplify your transition towards sustainability, ensuring a smooth and effective integration of eco-friendly practices.
Seek Professional Help Toward Sustainable Supply Chain
Embarking on the journey to decarbonise your supply chain is a commendable endeavour. While it presents challenges, trace. is here to guide you in finding solutions that align with your business goals. Partner with us for a seamless transition towards sustainability. Contact trace. today enquiries@traceconsultants.com.au.