Has it become normal in your organisation to rely on emergency processes, like expediting or airfreighting, rather than the exception? Are your employees struggling to provide consistent customer service, despite full warehouses of stock, or working additional hours? Many businesses today face similar challenges.
Rising mistrust in systems, use of manual overrides, and continual underperformance of new product launches signal inefficiencies within supply chains. This misalignment often leads to high levels of waste, lost sales, and diminished customer trust. Addressing these challenges requires not only identifying the symptoms but also taking a deeper dive into the root causes of supply chain misalignment. In this article, we focus on ways to identify the root causes of these problems, and how to take a structured approach to resolving them.
Common Indicators of Supply Chain Misalignment
Supply chain misalignment is often evident through symptoms that disrupt business efficiency. Key signs include:
- Rising use of overtime: Either at DCs or Plants, issues are being resolved with extra unplanned labour
- High levels of write-offs and waste: Inventory planning gaps leading to obsolete or expired stock
- Exceptions becoming the norm: Regular use of more expensive options to meet demand such as air freighting or transferring stock between locations
- Distribution centres (DCs) at capacity with lost sales: DC operations are overwhelmed yet unable to meet demand
- Eroding trust: A lack of confidence from suppliers and customers
- Mistrust in systems: Heavy reliance on human intervention and excessive manual checks
Getting to the Root Cause of Supply Chain Misalignment
To truly resolve inefficiencies in supply chain operations, it’s essential to go beyond surface-level issues and identify the root causes. Misalignments can stem from a combination of structural gaps and foundational capability weaknesses, which collectively impact overall performance. By dissecting these core elements, organisations can begin to understand the critical factors holding back their supply chain from optimal functionality.
Foundational Capabilities
- People: Does your organisation depend heavily on a few key individuals? Not only does this increase operational risk if those individuals are unavailable or leave the organisation, it can impede the organisation’s ability to undertake strategic projects
- Processes: Are supply chain processes well-defined and followed consistently? Knowledge sharing, documenting of processes and upskilling of the whole team is critical for delivering quality outcomes.
- Technology: Are current systems and tools fully integrated, and do they streamline key processes to support your supply chain? Relying on outdated or disconnected technologies can prevent seamless planning and execution.
- Data & Insights: Is your data accurate and timely? Are you spending more time collecting data than analysing it? Without reliable data, supply chain decisions may be based on incorrect assumptions, leading to misaligned strategies.
Structural Enablers
- Organisational Structure: Are roles and responsibilities within your supply chain clearly defined and aligned with your business model? An unbalanced structure can lead to inefficiencies or misalignment of goals and initiatives across the organisation.
- Governance: How are supply chain decisions made, and are they aligned with the broader business strategy? Effective governance is essential for coordinating activities across the supply chain and ensuring compliance with best practices.
- KPIs & Incentives: What behaviours are being driven by your current KPIs and incentive structures? Misaligned KPIs can encourage actions that may benefit short-term performance but harm long-term goals, such as overemphasis on production speed at the cost of quality or customer satisfaction. Are the right performance metrics in place to encourage collaboration, efficiency, and innovation across your supply chain?
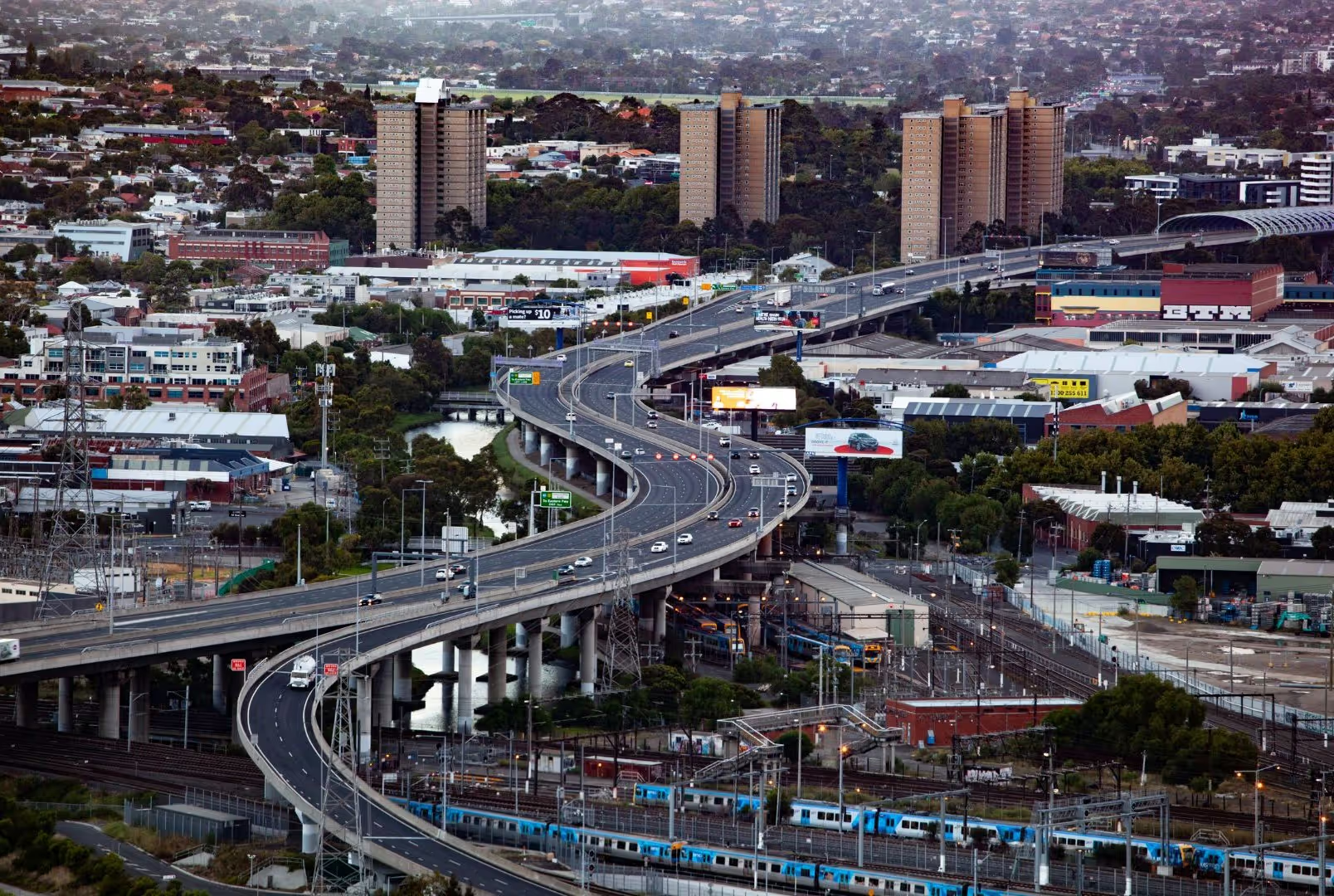
A Structured Approach to Supply Chain Planning Improvements
Effective supply chain transformation is rooted in a structured approach, designed to diagnose, design, develop, and deliver the necessary changes.
- Diagnose
The first step in any improvement initiative is diagnosing the current state of your supply chain. Key activities in this phase include:
- Business process discovery
- Issue, inefficiency, and bottleneck identification
- Root cause analysis
- Impact quantification
- Design
Once the root causes are identified, the next step is to design tailored solutions that address those gaps. Key activities may include:
- Target state capabilities determination
- Business process and capability roadmap development
- Solution architecture design
- Business case creation
- Develop
After designing the necessary improvements, the focus shifts to developing the solution. This involves the hands-on building and testing of new processes, systems, or tools. Key activities in this phase include:
- Solution build and test
- Capability development
- Pilot testing and deployment planning
- Deliver
The final phase is delivering the solution across the entire organisation. This requires careful management to ensure that the improvements are fully implemented and deliver the expected results. Key activities to support this phase include:
- Project management and implementation support
- Change management
- Results delivery and value realisation
Building the Business Case for Change
A robust business case forms the backbone of any successful supply chain transformation. This involves quantifying the expected benefits of improved planning capabilities.
- Current Capability Analysis: Evaluate the existing supply chain planning capabilities across people, processes, policies, and technology.
- Gap Modelling: Compare the organisation’s current capabilities to improved practices, suitable to the organisations size, investment appetite and perceived ROI, identifying the areas with the most potential for improvement.
- Targeted Business Case: Develop a business case that targets the most critical capability gaps and outlines the expected ROI.
Typical benefits of improving supply chain planning include:
- Revenue Growth: Increased sales through improved availability and forecasting.
- Cost Reduction: Lower inventory carrying costs and a healthier mix of inventory, reducing waste and obsolescence.
- Operational Efficiency: Better labour utilisation and fewer emergency orders due to enhanced capacity management.
- Optimised Working Capital: Streamlined inventory levels, supported by improved planning processes.
Next steps
Trace Consultants have the flexibility, knowledge, and experience to provide hands-on support across any or all steps in the Supply Chain Planning Improvement process. If your organisation is experiencing any of these symptoms or seeking ways to unlock value in your supply chain, contact the trace. team today.
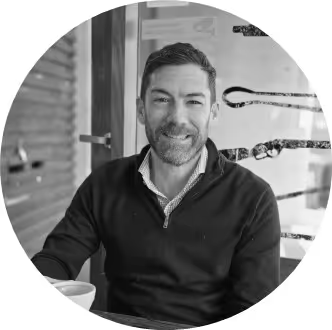
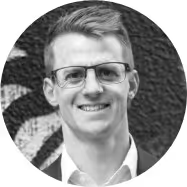
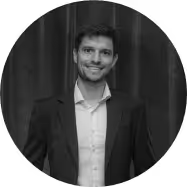
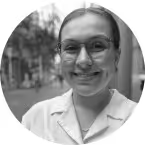