Back-of-house (BOH) supply chains are the invisible driving force behind many industries, including integrated resorts, food and beverage (F&B), retail, hospitals, and more. While customers rarely see BOH operations, their impact on the efficiency, safety, and profitability of front-end operations is undeniable. Poorly designed infrastructure in BOH areas often leads to inefficiencies, driving up costs and creating unsafe working environments. To avoid these pitfalls, businesses need to assess and address the complexities within their BOH supply chains, enabling long-term benefits such as scalability and adaptability to evolving organisational needs.
Understanding the Complexities of BOH Supply Chains
BOH logistics are complex and vary depending on the industry, yet certain challenges are universal. For example, hospitals need to manage clinical waste and ensure the timely delivery of critical supplies, while F&B businesses must juggle fresh produce management. These complexities require careful planning and consideration to maintain service levels and operational efficiency.
Here are some common complexities that impact BOH supply chains across industries:
Supplier Relationships and Coordination
Strong supplier relationships are essential for resilient supply chains, especially in BOH operations. Managing multiple vendors, ensuring consistent quality, and maintaining reliability are crucial for minimising disruptions. In industries like hospitality, retail, and healthcare, poor coordination can result in delayed deliveries, quality issues, and service bottlenecks, all of which negatively impact customer-facing operations.
Supply Chain Disruptions
External factors such as global pandemics, natural disasters, or geopolitical events can lead to significant disruptions. These disruptions often result in delays, increased costs, and product shortages, affecting inbound deliveries for hotels, hospitals, and entertainment venues. Without well-planned mitigation strategies, these disruptions can severely impact business continuity.
Sustainability Challenges
Sustainability is becoming a higher priority for organisations, adding another layer of complexity to BOH supply chains. The push to reduce carbon footprints, source locally, and minimise waste has implications for supplier selection, inventory management, and transport logistics. For example, hospitals must balance sustainability with regulatory compliance, while F&B and entertainment venues may need to find ways to reduce packaging waste or energy consumption.
Inventory Management
With a wide range of products stored across multiple locations, managing inventory is a critical challenge in BOH operations. Poor inventory management can lead to overstocking, spoilage, or understocking, all of which negatively affect operations. For example, an overstock of perishable goods in a hotel can lead to waste, while understocking clinical supplies in a hospital could endanger patient care.
Inbound Traffic and Congestion
Coordinating deliveries and outbound logistics across different locations can be a logistical nightmare, particularly in large venues like hospitals or resorts. Congested loading docks, traffic issues, and safety hazards can disrupt the flow of goods and cause delays. This is particularly problematic in high-volume environments where delays can lead to poor service outcomes and safety risks.
Demand Forecasting
Accurate demand forecasting is essential in preventing overstock and shortages, particularly during peak seasons or special events. Without reliable forecasting, F&B venues may find themselves with excess inventory, while hospitals may struggle to manage fluctuating demand for essential medical supplies, especially during critical periods.
Compliance and Regulations
BOH supply chains must navigate a myriad of regulatory challenges, from labour laws to environmental regulations. These regulations vary by industry and can impact everything from supplier selection to product handling and transportation. For example, hospitals face strict regulations around the handling of clinical waste, while F&B venues must comply with food safety standards.
The Risks of Ineffective BOH Supply Chains
When BOH logistics and supply chains are not optimised, the consequences can be severe, impacting financial performance, reputation, and even safety. Outdated infrastructure or poorly designed facilities often lead to operational workarounds that create inefficiencies. These inefficiencies are costly, labour-intensive, and can obscure the underlying problems, allowing them to persist.
Some of the risks of inadequate BOH operations include:
- Storage Capacity Issues: When storage areas reach capacity, inventory management becomes compromised, leading to poor stock quality, increased spoilage, and potential safety hazards.
- Rising Costs: Inefficiencies in the BOH supply chain often result in higher labour costs, as more staff are needed to manage inventory manually or rectify errors. Additionally, poor inventory practices can lead to wastage and damage, further increasing costs.
- Reduced Service Levels: Poor BOH operations can slow down the flow of goods and services to the front-end, causing delays in serving customers, whether it's delivering meals in a hotel or ensuring timely care in a hospital.
- Traffic Congestion: Congested BOH areas create inefficiencies in the movement of goods, impacting both inbound and outbound logistics. This can result in delays that disrupt overall operations, particularly during busy periods.
The Opportunities in Optimising BOH Supply Chains
While BOH supply chains are inherently complex, there are substantial opportunities for organisations to improve their operations through thoughtful design and optimisation. By addressing these complexities, businesses can create scalable, adaptable systems that meet their evolving needs while controlling costs and maintaining service levels.
Some key benefits of optimising BOH supply chains include:
- Scalable Infrastructure: Purpose-built infrastructure allows for flexibility and growth. A well-designed BOH area can support an agile operating model that evolves with the business, ensuring it can handle increases in demand or operational challenges with ease.
- Cost-Effective Operations: Efficient BOH systems reduce the need for manual workarounds, lowering labour costs and improving inventory management. This results in significant savings, especially in industries like healthcare and hospitality, where the cost of inefficiency can be high.
- Improved Service Levels: A streamlined BOH supply chain ensures that the flow of goods and services is uninterrupted, leading to faster turnaround times for customers and higher service satisfaction. This is critical in environments like hospitals or F&B establishments, where service quality directly impacts customer outcomes.
- Enhanced Resilience: By addressing potential disruptions and planning for sustainability, organisations can ensure their BOH operations are resilient, even in the face of challenges like supply chain disruptions or regulatory changes.
Next Steps for Optimising BOH Supply Chains
For organisations looking to address the complexities in their BOH operations, a structured approach is key. The following steps can help organisations begin their journey towards optimised BOH supply chains:
- Diagnostic Review: Start with a high-level diagnostic of your current BOH operations to identify key issues and opportunities. Understanding the root causes of inefficiencies is essential for determining where improvements can be made.
- Engage Cross-Functional Teams: Involve stakeholders from various departments to ensure that the entire organisation's needs are considered in the redesign of BOH operations. A cross-functional team will bring valuable insights from different areas of the business.
- Seek External Expertise: Engaging external consultants like Trace Consultants can provide an objective perspective and bring industry best practices to the table. External experts can help refine the business case for change, identifying the most effective solutions for your specific needs.
- Develop a Transition Plan: Create a roadmap that outlines short-, medium-, and long-term improvements. This plan should address key areas such as people, processes, technology, and infrastructure, ensuring that all aspects of the BOH supply chain are aligned with the organisation’s goals.
- Execute and Monitor Progress: Build a dedicated team to execute the transition plan, monitoring progress closely and adjusting as needed. Sharing successes along the way will keep momentum going and ensure organisational buy-in.
How Trace Consultants Can Help
Optimising BOH supply chains requires deep expertise and a tailored approach to each organisation’s unique challenges. At Trace, we specialise in helping organisations across various sectors, including hospitals, F&B, and entertainment venues, improve their BOH logistics and supply chains. Our team offers:
- Comprehensive Diagnostics: We begin by conducting a thorough assessment of your BOH operations, identifying inefficiencies and opportunities for improvement.
- Bespoke Solutions: Using our extensive industry knowledge, we design solutions that address the specific challenges of your organisation, whether it’s reducing costs, improving service levels, or navigating regulatory requirements.
- Cross-Functional Support: Our approach integrates people, processes, and technology to ensure that all aspects of the BOH supply chain are optimised.
- Long-Term Value: We help you develop scalable, future-proofed supply chain solutions that adapt to changes in demand and the broader market environment.
With Trace Consultants by your side, your organisation can transform its BOH operations, delivering cost savings, improved efficiency, and better service outcomes. Contact us today to start your journey toward BOH supply chain optimisation.
Contact us today, trace. your supply chain and procurement consulting partner.
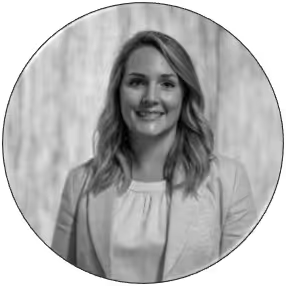
Emma Woodberry
Senior Manager
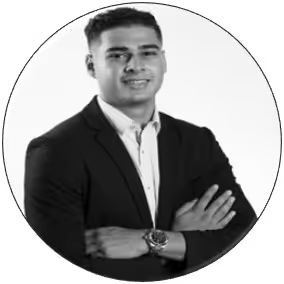
Prajin Shah
Senior Consultant