Advanced Planning Systems (APS), such as SAP's Advanced Planner and Optimizer (APO), Oracle's Advanced Supply Chain Planning (ASCP), and Kinaxis RapidResponse, are integral to modern businesses. They offer robust solutions for accurate forecasting, efficient inventory management, and streamlined resource allocation. However, successful implementation of these systems on a large scale can be challenging and complex. This article delves into how an adept supply chain project manager can play a pivotal role in ensuring a successful APS implementation.
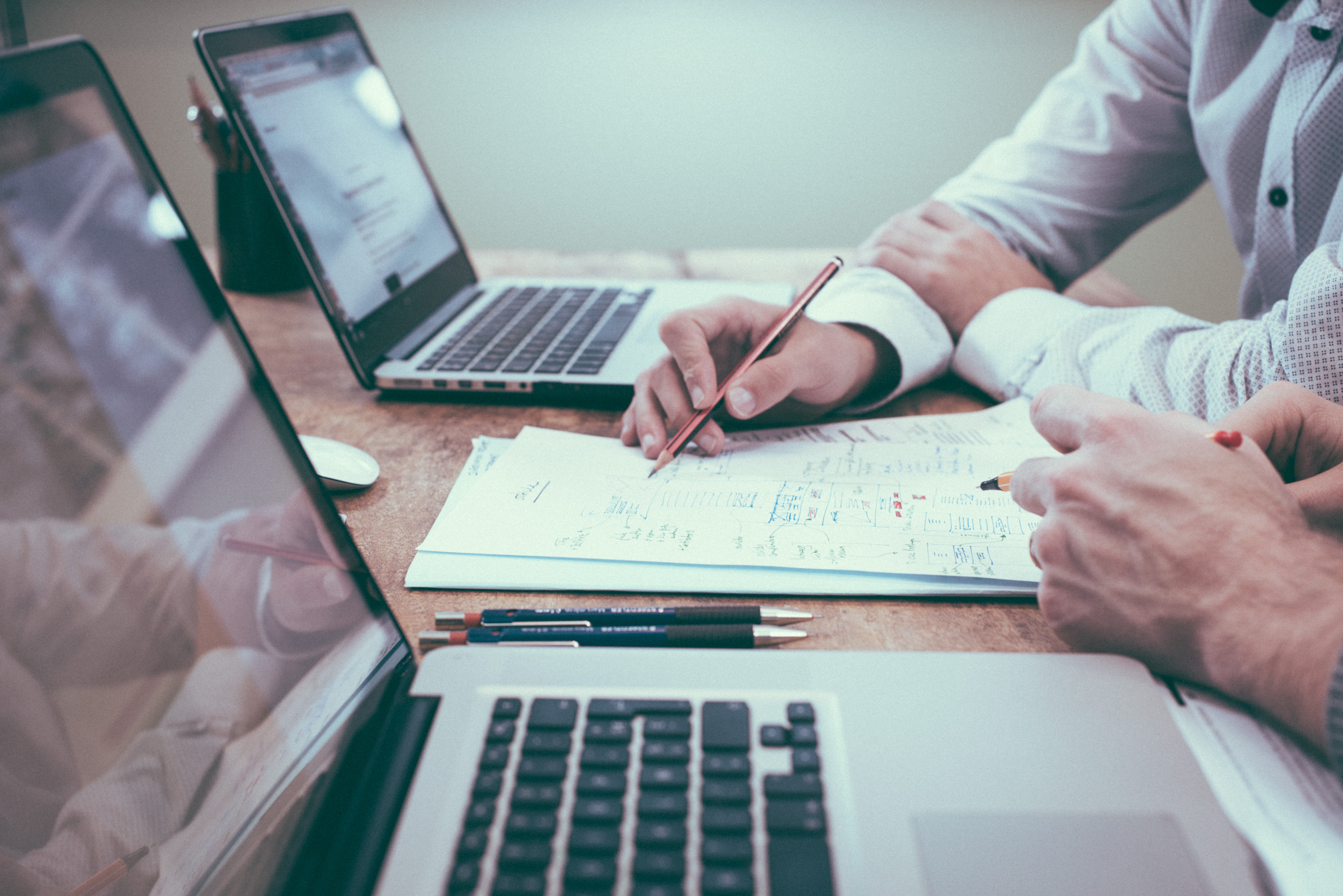
n today's marketplace, a wide array of Advanced Planning Systems is available, each with unique features and capabilities. Notable systems include SAP's Advanced Planner and Optimizer (APO), Oracle's Advanced Supply Chain Planning (ASCP), Kinaxis RapidResponse, JDA Demand Planning, I2 Technologies' Supply Chain Planner, Logility's Voyager Solutions, Infor's Supply Chain Planning, Demand Solutions' DSX platform, Blue Yonder's Luminate Planning, and Epicor's SCM software.
Selecting the right product from this vast range is a critical starting point in the project management process. An effective project manager understands that this decision should be based on a thorough analysis of the organisation's unique needs, existing infrastructure, and strategic goals. They work closely with stakeholders to define system requirements, conduct a comprehensive market review, and evaluate potential solutions based on their suitability, cost-effectiveness, scalability, and integration capabilities.
The project manager's role doesn't end with product selection. Instead, this is where their journey begins, laying the groundwork for a successful implementation. They work towards aligning stakeholders, defining clear project timelines, and outlining key deliverables to ensure the chosen APS meets the organisation's strategic objectives and delivers maximum value.
Navigating the Complex Landscape of APS Implementation
Large-scale APS implementations encompass an array of components, including hardware and software integration, process changes, and human resources management. An experienced supply chain project manager, equipped with an intricate understanding of these elements, can navigate this complex landscape. They ensure the seamless integration of all components, orchestrating them into a functioning, cohesive system that aligns with the organisational goals.
Proactively Managing Risks
Any large-scale project is susceptible to various risks, and APS implementations are no different. Skilled project managers are adept at identifying and assessing potential risks at early stages. They devise effective contingency plans and swiftly act to mitigate risks, thereby averting delays, cost escalations, and other challenges that may hinder the smooth execution of the project.
Facilitating Alignment Among Internal Stakeholders and External Vendors
One of the critical roles of a project manager is bridging the gap between diverse stakeholders. These can range from top management and internal IT teams to end-users and external APS partners such as SAP, Oracle, or Kinaxis. The project manager ensures that all these entities align with the project's objectives, timelines, and expected outcomes, fostering a collaborative environment crucial for the successful implementation of an APS.
Leading Change Management Efforts
The integration of a new APS often necessitates significant changes in existing procedures, roles, and workflows. Project managers, backed by their change management expertise, are instrumental in steering this transition. They formulate and execute comprehensive change management plans to ensure that all stakeholders comprehend and adapt to the new system effectively and efficiently.
Optimising Value Delivery
An experienced project manager recognises how to maximise the value derived from an APS. They align the capabilities of the system with the strategic objectives of the business, ensuring effective utilisation and continuous monitoring of the system's performance post-implementation.
The successful implementation of a large-scale APS, like SAP APO, Oracle ASCP, or Kinaxis RapidResponse in Australia, relies significantly on the competence of an experienced supply chain project manager. Their specialised skills and knowledge enable them to navigate project complexities, manage risks, synchronise stakeholders, lead change, and ensure the delivery of substantial value to the organisation.
Contact us today, trace. your supply chain consulting partner.