In the demanding environment of healthcare, the efficiency of back-of-house logistics is critical. This aspect of hospital operations often goes unnoticed but is crucial in ensuring that front-line staff can deliver high-quality patient care. From the design of consumable stores, central stores, and loading docks to production kitchens, linen stores, and waste stores, the physical spaces and their associated operating models play a significant role in the overall functionality and efficiency of healthcare facilities. This article explores the importance of these elements and how optimising them can enhance hospital operations. Additionally, it highlights how Trace Consultants can work alongside architects and project manager firms to ensure development projects deliver on the desired outcomes for government agencies, hospitals, clinicians, and patients.
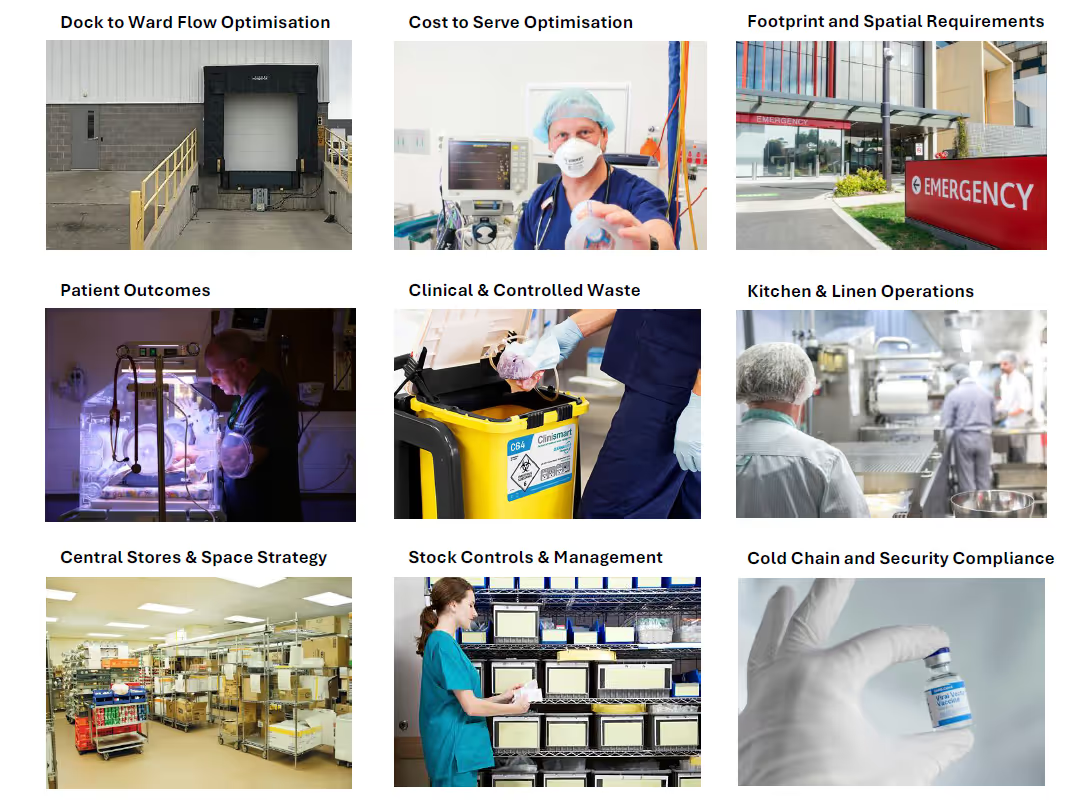
The Importance of Back-of-House Logistics
Enhancing Operational Efficiency
Back-of-house logistics encompass all the activities that support the front-line healthcare staff, including inventory management, procurement, and supply chain operations. Efficient logistics ensure that medical supplies, equipment, and other necessary items are available when needed, reducing delays and improving patient care.
Reducing Operational Costs
Optimising logistics can significantly reduce operational costs. By streamlining processes, hospitals can minimise waste, reduce excess inventory, and improve the utilisation of resources. This not only lowers costs but also ensures that funds can be redirected towards patient care and other critical areas.
Improving Patient Care
Effective logistics directly impact patient care by ensuring that healthcare providers have the necessary tools and supplies at their disposal. This reduces the time spent searching for items, allowing more time for patient interaction and care. Additionally, well-organised logistics help prevent errors and ensure the timely delivery of services.
Optimising the Physical Design of Spaces
Consumable Stores
Consumable stores must be designed to facilitate easy access and efficient inventory management. Shelving, labelling, and storage systems should be optimised to ensure that items are easy to find and retrieve. This reduces the time staff spend searching for supplies and minimises the risk of errors.
Central Stores
Central stores are the hub of hospital logistics. They should be strategically located and designed to support the efficient flow of goods throughout the hospital. This includes adequate space for receiving, storing, and distributing supplies. An optimised central store layout reduces the time and effort required to move items to their final destinations.
Loading Docks
Loading docks are the entry points for supplies entering the hospital. Their design should facilitate the smooth and efficient unloading of goods. This includes considering factors such as dock height, access for delivery vehicles, and proximity to storage areas. An efficient loading dock design minimises delays and ensures a steady flow of supplies.
Production Kitchens
Production kitchens must be designed to support the efficient preparation and delivery of meals to patients. This includes optimising the layout for workflow, ensuring adequate storage for ingredients, and implementing systems for managing dietary requirements and food safety. A well-designed production kitchen improves meal service efficiency and patient satisfaction.
Linen Stores
Linen stores should be organised to facilitate easy access to clean linens and efficient collection of soiled items. This includes considering factors such as shelving, labelling, and cart systems for transporting linens. An optimised linen store design reduces the time and effort required to manage linens and ensures that clean items are always available when needed.
Waste Stores
Waste stores must be designed to support the safe and efficient disposal of medical waste. This includes providing adequate space for different types of waste, implementing systems for segregation and disposal, and ensuring easy access for waste collection services. An efficient waste store design improves safety and compliance with regulations.
Operating Model Design
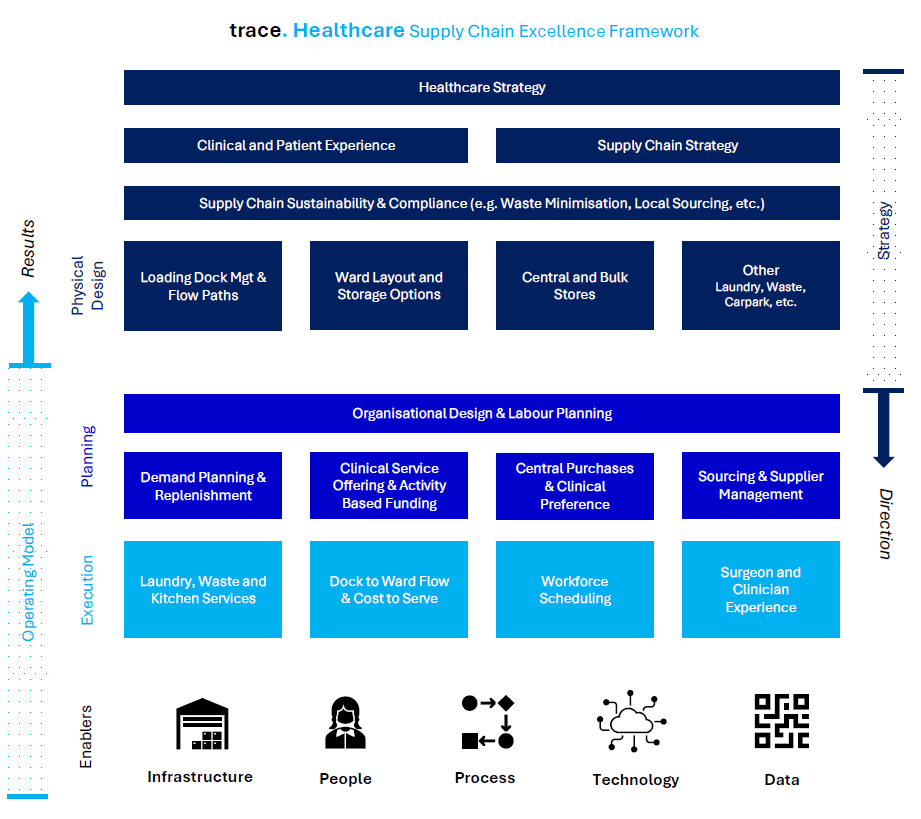
Inventory Management
Effective inventory management is crucial for ensuring that supplies are available when needed without overstocking. This includes implementing systems for tracking inventory levels, forecasting demand, and automating reordering processes. Optimising inventory management reduces costs, minimises waste, and ensures the timely availability of supplies.
Demand Planning
Accurate demand planning is essential for matching supply with demand. This includes analysing historical data, monitoring current usage patterns, and forecasting future needs. Effective demand planning helps prevent shortages and overstocking, ensuring that resources are used efficiently.
Stocking Policy
A well-defined stocking policy ensures that critical items are always available while minimising excess inventory. This includes setting minimum and maximum stock levels, implementing systems for monitoring stock levels, and establishing procedures for reordering supplies. An optimised stocking policy improves inventory management and reduces costs.
Procurement Processes
Efficient procurement processes ensure that supplies are purchased at the best possible prices and delivered on time. This includes negotiating contracts with suppliers, implementing systems for managing orders, and monitoring supplier performance. Optimising procurement processes reduces costs and ensures the timely availability of supplies.
Labour Planning
Effective labour planning ensures that the right number of staff are available to meet demand. This includes forecasting staffing needs, scheduling shifts, and implementing systems for managing attendance and performance. Optimising labour planning improves efficiency and reduces labour costs.
Asset Management
Efficient asset management ensures that equipment and other assets are properly maintained and utilised. This includes implementing systems for tracking assets, scheduling maintenance, and managing asset lifecycles. Optimising asset management reduces costs and improves the availability and reliability of equipment.
Dock Scheduling and Management
Effective dock scheduling and management ensure that supplies are delivered and unloaded efficiently. This includes implementing systems for scheduling deliveries, managing dock operations, and monitoring performance. Optimising dock scheduling and management reduces delays and ensures a steady flow of supplies.
How Trace Consultants Can Help
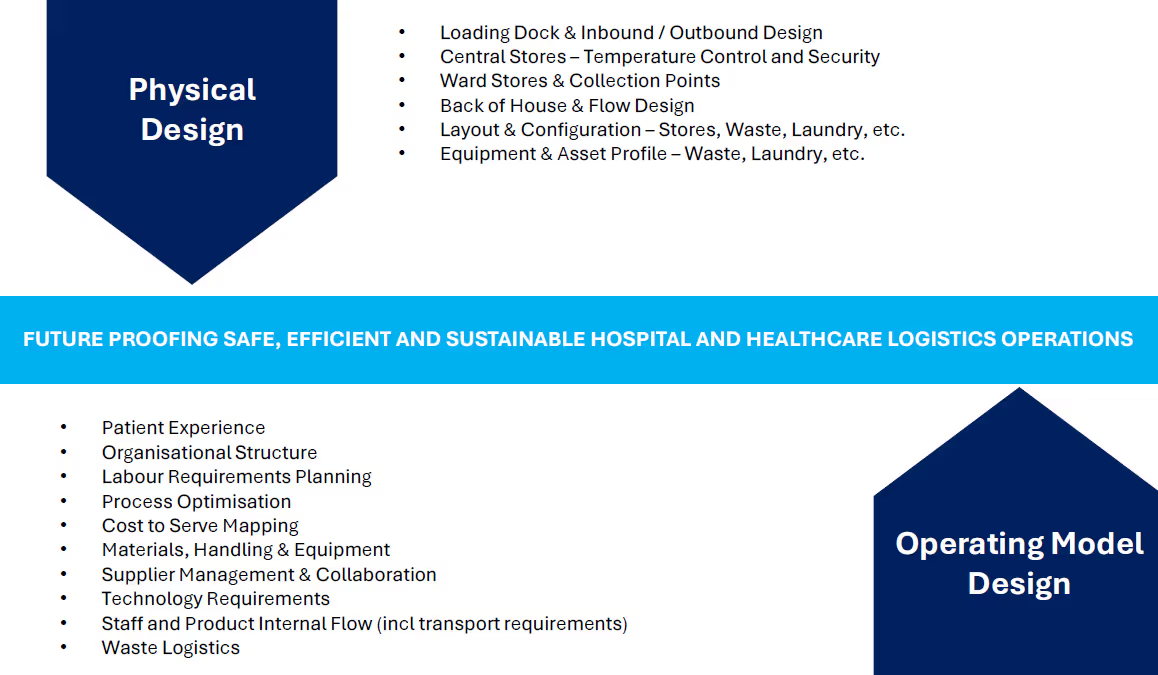
Collaboration with Architects and Project Managers
Trace Consultants can work alongside architects and project manager firms to ensure that development projects deliver on the desired outcomes for government agencies, hospitals, clinicians, and patients. This includes:
Strategic Planning
Trace Consultants can assist with strategic planning to determine the core requirements of a project. This includes conducting feasibility studies, developing business cases, and engaging with stakeholders to ensure that the project meets the needs of the organisation.
Clinical and Infrastructure Asset Audits
Trace Consultants can conduct clinical and infrastructure asset audits to assess the current state of facilities and identify areas for improvement. This includes reviewing compliance with regulations, assessing the condition of assets, and identifying opportunities for optimisation.
Concept Brief Development
Trace Consultants can assist with developing concept briefs to inform master plans. This includes defining the scope of the project, identifying key objectives, and outlining the requirements for facilities and services.
Master Plan Strategic Advisory
Trace Consultants can provide strategic advisory services for master plans. This includes analysing data, assessing the feasibility of different options, and providing recommendations for optimising facilities and services.
Service Delivery Model Documentation
Trace Consultants can assist with documenting service delivery models. This includes defining the operational model, identifying key processes, and developing procedures for managing services. This helps ensure that the project meets the needs of the organisation and delivers the desired outcomes.
User Group Facilitation
Trace Consultants can facilitate user group meetings during all aspects of planning and design. This includes engaging with stakeholders, gathering feedback, and resolving issues that arise during the planning and design process. This helps ensure that the project meets the needs of the organisation and delivers the desired outcomes.
Facility and Operational Commissioning
Trace Consultants can assist with facility and operational commissioning. This includes developing commissioning plans, coordinating activities, and ensuring that facilities and services are ready for operation. This helps ensure that the project meets the needs of the organisation and delivers the desired outcomes.
Post Occupancy Evaluation
Trace Consultants can conduct post-occupancy evaluations to assess the performance of facilities and services. This includes gathering feedback from users, analysing data, and identifying opportunities for improvement. This helps ensure that the project meets the needs of the organisation and delivers the desired outcomes.
Case Studies
Case Study 1: Optimising a Central Store Layout
A large hospital in Australia faced challenges with its central store layout, leading to inefficiencies and delays in the delivery of supplies. Trace Consultants were engaged to redesign the layout and optimise inventory management processes. By implementing a new shelving system, improving labelling, and reorganising the flow of goods, the hospital was able to reduce the time taken to retrieve items and improve overall efficiency. The project resulted in significant cost savings and improved staff satisfaction.
Case Study 2: Enhancing Linen Store Management
A regional hospital struggled with managing its linen stores, leading to frequent shortages and increased operational costs. Trace Consultants were engaged to optimise the design of the linen stores and implement new management processes. By introducing a new cart system, improving labelling, and implementing a just-in-time inventory system, the hospital was able to reduce costs and ensure the timely availability of clean linens. The project improved efficiency and enhanced patient care.
Case Study 3: Improving Waste Management Systems
A metropolitan hospital faced challenges with its waste management systems, leading to compliance issues and increased costs. Trace Consultants were engaged to redesign the waste stores and implement new management processes. By improving the layout of the waste stores, introducing new segregation systems, and implementing a waste tracking system, the hospital was able to improve compliance and reduce costs. The project resulted in a safer and more efficient waste management system.
Optimising hospital back-of-house logistics and the physical design of spaces is crucial for improving operational efficiency, reducing costs, and enhancing patient care. By focusing on areas such as consumable stores, central stores, loading docks, production kitchens, linen stores, and waste stores, hospitals can ensure that they are well-equipped to meet the demands of healthcare delivery. Additionally, effective operating model design in areas such as inventory management, demand planning, stocking policy, procurement processes, labour planning, asset management, and dock scheduling and management is essential for ensuring the smooth and efficient operation of hospital logistics.
Trace Consultants, with their expertise in supply chain consulting, can work alongside architects and project manager firms to ensure that development projects deliver on the desired outcomes for government agencies, hospitals, clinicians, and patients. Through strategic planning, clinical and infrastructure asset audits, concept brief development, master plan strategic advisory, service delivery model documentation, user group facilitation, facility and operational commissioning, and post-occupancy evaluation, Trace Consultants can help optimise hospital logistics and physical design, ultimately leading to improved healthcare outcomes.
In conclusion, the importance of hospital back-of-house logistics and optimising the physical design of spaces cannot be overstated. By focusing on these critical areas and leveraging the expertise of Trace Consultants, hospitals can achieve significant improvements in efficiency, cost savings, and patient care.
How can your hospital benefit from optimising its back-of-house logistics and physical design?