Why Supply Chain Network Optimisation is More Critical Than Ever
In an era of rising costs, shifting global trade policies, and evolving customer expectations, supply chain leaders are under increasing pressure to optimise their networks. Organisations are grappling with fixed and variable cost pressures, transport inefficiencies, and operational bottlenecks that threaten profitability and service levels.
To delve deeper into these challenges, we sat down with Shanaka Jayasinghe, Partner at Trace Consultants, to discuss how organisations can unlock cost savings, reduce risk, and gain a competitive advantage through strategic supply chain network design and optimisation.
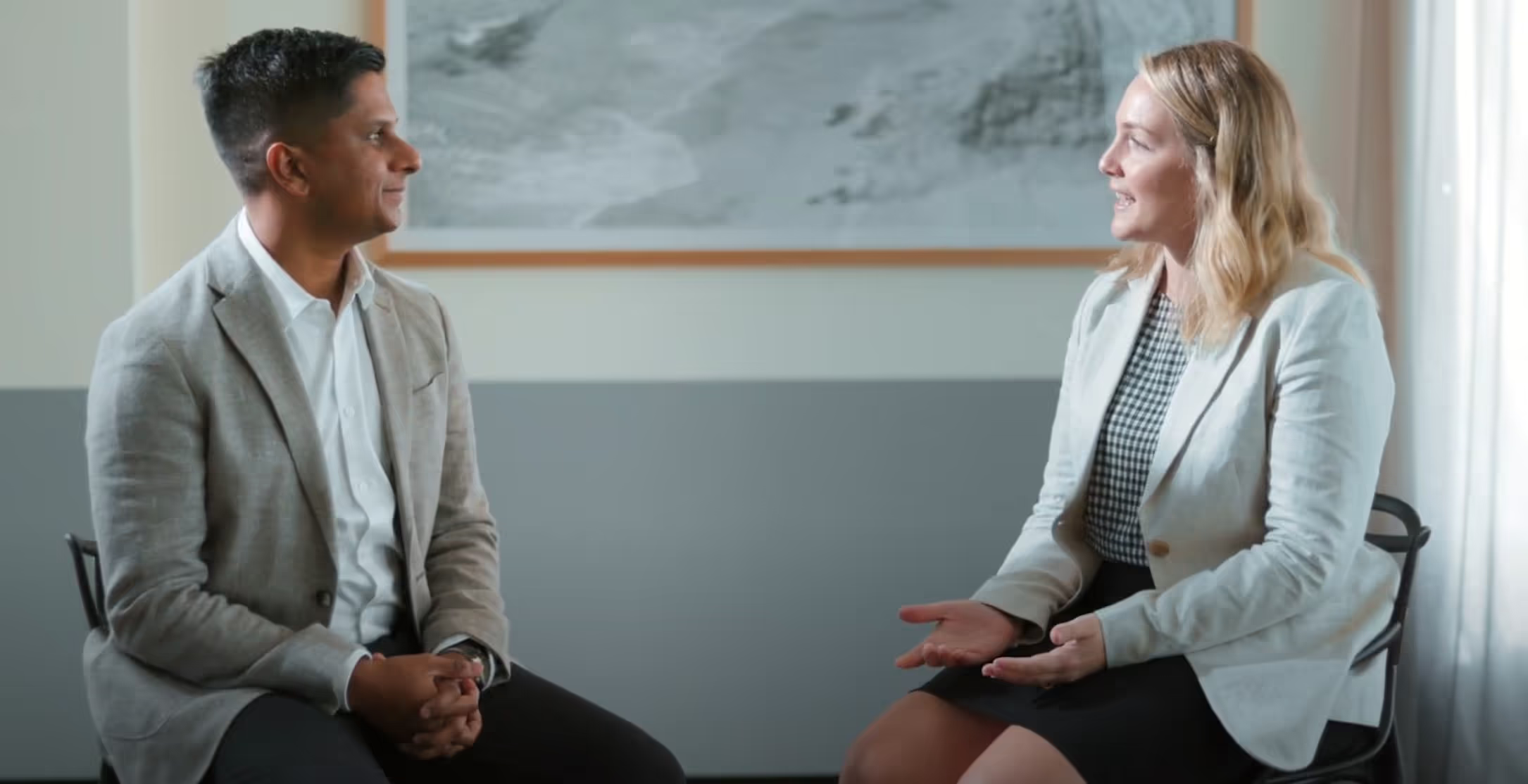
Interview with Shanaka Jayasinghe
Q: Why is warehouse network optimisation such a critical priority for organisations today?
Shanaka Jayasinghe:
The supply chain landscape has changed dramatically over the last few years. Businesses are facing inflationary pressures, volatile demand patterns, supply disruptions, and rising transport costs. At the same time, customers expect faster and more reliable deliveries.
Warehouse network optimisation is critical because it directly impacts an organisation’s cost structure and service performance. A well-designed network can unlock fixed cost reductions (through footprint rationalisation), variable cost efficiencies (through better labour and space utilisation), and transport cost savings (through better network flow and distribution planning).
For example, we recently worked with an FMCG client whose warehouse footprint was misaligned to their demand centres—leading to excessive transport costs and stockouts. By redesigning their distribution network and optimising their hub-and-spoke model, we reduced their transport costs by 18% while improving service levels.
Q: Many organisations struggle with outdated supply chain infrastructure. When should a company conduct a strategic supply chain review?
Shanaka Jayasinghe:
There are a few key triggers that indicate an organisation needs a strategic supply chain review:
- Cost Pressures & Margin Erosion – If warehousing, transport, or inventory carrying costs are rising disproportionately.
- Service Failures & Customer Complaints – If lead times are increasing, OTIF (On-Time In-Full) metrics are declining, or stock availability is inconsistent.
- Growth & Expansion – If a company is expanding into new markets, launching new products, or experiencing rapid demand changes.
- Technology & Automation Initiatives – If an organisation is investing in warehouse automation, robotics, or predictive analytics but lacks an optimised network to fully leverage these capabilities.
- M&A Activity & Business Restructuring – If an organisation has merged with or acquired another business and needs to integrate its supply chain.
At Trace Consultants, we help businesses conduct fact-based supply chain strategic reviews to assess their current network, identify inefficiencies, and design an optimised, future-ready supply chain.
Q: How can warehouse and transport design drive a competitive advantage?
Shanaka Jayasinghe:
A well-structured warehouse and transport strategy is no longer just about cost efficiency—it’s a competitive differentiator. Organisations that invest in strategic network design and warehouse optimisation can:
- Reduce working capital by optimising stock flow and reducing excess inventory.
- Improve service levels with faster delivery times and better inventory availability.
- Minimise waste by reducing handling, storage, and stock obsolescence.
- Increase labour productivity by streamlining warehouse layouts and automation solutions.
- Enhance supply chain resilience by diversifying risk across multiple locations.
One of our clients in the retail sector was struggling with stock imbalances across its warehouse network. High-demand SKUs were often understocked in key locations, while slower-moving items occupied valuable space in distribution centres. We designed an optimised inventory allocation model and restructured their warehouse-to-store distribution flows, which resulted in a 25% improvement in shelf availability and a 14% reduction in working capital.
Q: What are the most common bottlenecks in manufacturing and distribution networks?
Shanaka Jayasinghe:
The most common bottlenecks we see include:
- Inefficient Facility Layouts – Poorly designed warehouses lead to excessive material handling, congestion, and slow throughput.
- Poor Demand-Supply Matching – Many companies struggle with demand forecasting and inventory allocation, leading to either overstocking or stockouts.
- High Freight Costs & Inefficient Transport Routes – Without optimised transport planning, organisations incur excessive last-mile delivery costs and inefficiencies in freight consolidation.
- Over-Reliance on Manual Processes – Many warehouses still rely on paper-based systems or legacy technology that limits scalability and efficiency.
- Lack of Visibility & Data Analytics – Without real-time supply chain visibility, organisations struggle to proactively identify risks and inefficiencies.
The good news is that these bottlenecks can be systematically addressed through a structured approach to supply chain network optimisation.
Q: How can supply chain network design reduce risk and improve service levels?
Shanaka Jayasinghe:
A resilient supply chain must be flexible, agile, and well-diversified. By investing in strategic network design, organisations can:
- Reduce dependency on single suppliers or warehouses and build contingency plans.
- Enhance supply chain redundancy to mitigate risks of disruption from natural disasters, geopolitical risks, or supplier failures.
- Improve response times through strategically located distribution centres closer to demand centres.
- Leverage multi-modal transport strategies to improve agility in case of disruptions.
During the pandemic, one of our manufacturing clients faced severe disruptions because 70% of their inbound materials came from a single offshore supplier. By reconfiguring their supplier network and implementing nearshoring strategies, they were able to reduce lead time variability by 40% and lower supply risk exposure.
Q: How will trade wars and tariffs impact supply chain infrastructure and networks?
Shanaka Jayasinghe:
Trade policies, tariffs, and geopolitical tensions are already reshaping global supply chains. Many organisations are re-evaluating their offshore supply strategies due to increased import costs, regulatory uncertainty, and the need for greater resilience.
Key trends we are seeing include:
- A shift towards regionalisation and nearshoring to reduce dependency on overseas suppliers.
- Increased investment in dual-sourcing strategies to diversify risk.
- Reassessing warehouse and distribution networks to mitigate tariff impacts.
- Exploring alternative trade agreements to optimise duty structures.
At Trace Consultants, we help businesses model different supply chain scenarios to evaluate cost and risk trade-offs in the face of geopolitical shifts.
Supply chain network optimisation is no longer just a cost-cutting exercise—it’s a strategic imperative that determines service capability, risk resilience, and long-term competitiveness.
For organisations looking to reduce costs, improve service levels, and future-proof their supply chain, the time to act is now.
Want to discuss how Trace Consultants can help? Get in touch today.