In today’s fast-paced and highly competitive business environment, efficient warehousing is crucial for operational success. The right warehouse design, coupled with advanced automation and optimised workflows, can significantly enhance productivity, reduce costs, and improve customer satisfaction. This article delves into the key aspects of warehouse design, explores the benefits of warehouse automation, and outlines strategies for optimising warehouse workflows and processes. Additionally, it highlights the importance of maintaining a safe working environment within the warehouse.
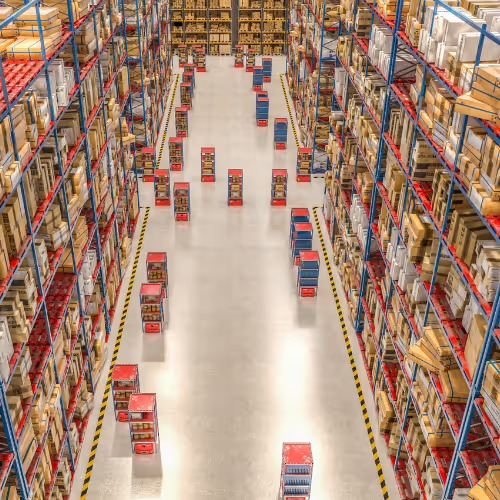
The Foundation: Effective Warehouse Design
1. Understanding Warehouse Design Principles
Warehouse design is the backbone of efficient warehousing. A well-designed warehouse maximises space utilisation, enhances workflow, and ensures safety. Key principles of warehouse design include:
- Layout Planning: The layout should facilitate smooth movement of goods and minimise handling. This involves strategic placement of receiving, storage, picking, packing, and shipping areas.
- Space Utilisation: Efficient use of vertical and horizontal space is crucial. This can be achieved through proper shelving, racking systems, and mezzanine floors.
- Accessibility and Safety: Ensuring easy access to goods and maintaining safety standards is vital. Aisles should be wide enough for equipment and personnel, and safety measures should be in place to prevent accidents.
2. Types of Warehouse Layouts
Different types of warehouse layouts serve various operational needs. Common layouts include:
- U-Shaped Layout: Ideal for warehouses with high throughput. It minimises travel distance by placing receiving and shipping areas next to each other.
- L-Shaped Layout: Suitable for warehouses with limited space. It offers flexibility in handling different types of goods.
- Straight Layout: Used in large warehouses where goods need to flow linearly from receiving to shipping.
3. Key Design Elements
Several design elements contribute to an efficient warehouse:
- Receiving Area: This area should be spacious enough to handle incoming goods and equipped with proper unloading facilities.
- Storage Systems: The choice of storage systems, such as pallet racking, shelving, or automated storage and retrieval systems (AS/RS), depends on the types of goods and inventory turnover.
- Picking Area: Designed for efficiency, the picking area should minimise travel time and facilitate accurate order picking.
- Packing and Shipping Area: Adequate space and equipment for packing and shipping ensure quick and error-free order fulfilment.
Embracing the Future: Warehouse Automation
1. Benefits of Warehouse Automation
Warehouse automation involves the use of technology to perform tasks that were traditionally done manually. The benefits of automation include:
- Increased Efficiency: Automated systems can operate 24/7, significantly increasing throughput and reducing labour costs.
- Improved Accuracy: Automation reduces human error, leading to more accurate order fulfilment and inventory management.
- Enhanced Safety: Automation reduces the risk of workplace injuries by handling heavy lifting and repetitive tasks.
- Scalability: Automated systems can be scaled up or down based on demand, offering flexibility in operations.
2. Types of Warehouse Automation
Various types of warehouse automation can be implemented depending on the specific needs and budget of an organisation:
- Automated Storage and Retrieval Systems (AS/RS): These systems use robots to store and retrieve goods, maximising space utilisation and reducing picking times.
- Conveyor Systems: Conveyors automate the movement of goods within the warehouse, streamlining processes and reducing manual handling.
- Automated Guided Vehicles (AGVs): AGVs transport goods within the warehouse autonomously, improving efficiency and reducing the need for manual forklifts.
- Robotic Picking Systems: These systems use robots equipped with vision systems to identify and pick items, increasing speed and accuracy.
- Warehouse Management Systems (WMS): A WMS integrates with other automated systems to manage inventory, track goods, and optimise workflows.
3. Implementing Automation: Key Considerations
When implementing warehouse automation, several factors need to be considered:
- Initial Investment: Automation requires significant upfront investment. A cost-benefit analysis should be conducted to ensure long-term ROI.
- Integration: Automated systems need to be integrated with existing warehouse management software and processes.
- Training: Employees need to be trained to work alongside automated systems and manage them effectively.
- Maintenance: Regular maintenance is crucial to keep automated systems running smoothly and prevent downtime.
Streamlining Operations: Warehouse Workflow and Process Optimisation
1. Understanding Warehouse Workflows
Warehouse workflows encompass all the processes involved in receiving, storing, picking, packing, and shipping goods. Optimising these workflows can lead to significant improvements in efficiency and productivity.
2. Key Workflow Optimisation Strategies
a. Lean Warehousing
Lean warehousing principles focus on eliminating waste and maximising value. Key elements include:
- 5S Methodology: This involves sorting, setting in order, shining, standardising, and sustaining to maintain an organised and efficient warehouse.
- Value Stream Mapping: Identifying and analysing all steps in the warehouse processes to eliminate non-value-added activities.
- Continuous Improvement: Encouraging a culture of continuous improvement where employees are empowered to identify and solve inefficiencies.
b. Slotting Optimisation
Slotting optimisation involves strategically placing inventory in the warehouse to minimise travel time and improve picking efficiency. Key considerations include:
- ABC Analysis: Classifying inventory into categories based on picking frequency (A: high frequency, B: moderate frequency, C: low frequency) and placing them accordingly.
- Product Dimensions: Ensuring items are stored in appropriately sized slots to maximise space utilisation.
- Seasonal Demand: Adjusting slotting based on seasonal demand patterns to ensure high-demand items are easily accessible.
c. Order Picking Strategies
Efficient order picking is crucial for timely order fulfilment. Strategies include:
- Batch Picking: Picking multiple orders simultaneously to reduce travel time.
- Zone Picking: Assigning pickers to specific zones within the warehouse to minimise movement.
- Wave Picking: Scheduling picking activities in waves based on order priorities and shipping schedules.
d. Technology Integration
Integrating technology can significantly enhance workflow optimisation:
- Warehouse Management Systems (WMS): A WMS can automate and optimise inventory management, order processing, and workflow planning.
- Barcode and RFID Technology: Using barcode and RFID systems for tracking inventory and streamlining picking and packing processes.
- Voice Picking Systems: Voice-directed picking systems guide workers through tasks using voice commands, increasing accuracy and efficiency.
3. Continuous Improvement and Monitoring
Optimising warehouse workflows is an ongoing process. Continuous monitoring and improvement are essential for maintaining efficiency. Key practices include:
- Performance Metrics: Tracking key performance indicators (KPIs) such as order accuracy, picking speed, and inventory turnover to identify areas for improvement.
- Employee Feedback: Regularly gathering feedback from employees to identify bottlenecks and inefficiencies in workflows.
- Technology Upgrades: Keeping up with advancements in warehouse technology to implement new solutions that enhance efficiency.
Prioritising Warehouse Safety
1. The Importance of Warehouse Safety
Maintaining a safe working environment in a warehouse is paramount. Safety not only protects employees from harm but also ensures smooth and efficient operations. An unsafe warehouse can lead to accidents, injuries, and even fatalities, which can disrupt operations and lead to legal and financial repercussions.
2. Key Elements of Warehouse Safety
a. Safety Training
Regular safety training is essential for all warehouse employees. Training should cover:
- Hazard Identification: Educating employees on how to identify potential hazards in the warehouse.
- Proper Equipment Use: Training on the safe operation of warehouse equipment such as forklifts, pallet jacks, and conveyor systems.
- Emergency Procedures: Ensuring employees know what to do in case of emergencies such as fires, chemical spills, or injuries.
b. Personal Protective Equipment (PPE)
Providing and enforcing the use of appropriate PPE is crucial. This includes:
- High-Visibility Clothing: Ensures employees are easily seen, reducing the risk of accidents.
- Safety Shoes: Protects feet from heavy objects and sharp items.
- Hard Hats: Protects heads from falling objects.
- Gloves and Eye Protection: Prevents injuries from handling materials and exposure to harmful substances.
c. Equipment Maintenance
Regular maintenance of warehouse equipment is essential to ensure it operates safely. This includes:
- Routine Inspections: Regularly checking equipment for signs of wear and tear.
- Scheduled Maintenance: Performing maintenance according to the manufacturer’s recommendations.
- Prompt Repairs: Addressing any equipment issues immediately to prevent accidents.
d. Safe Material Handling
Proper material handling practices reduce the risk of injuries. Key practices include:
- Manual Handling Techniques: Training employees on safe lifting and carrying techniques to prevent musculoskeletal injuries.
- Mechanical Aids: Using equipment such as forklifts and pallet jacks to handle heavy or bulky items.
- Safe Stacking and Storage: Ensuring materials are stacked and stored safely to prevent falls and collapses.
3. Safety Audits and Inspections
Regular safety audits and inspections help identify and address potential hazards before they cause harm. Key actions include:
- Routine Safety Audits: Conducting regular audits to assess the overall safety of the warehouse.
- Daily Inspections: Performing daily inspections of equipment and work areas to identify immediate hazards.
- Incident Investigations: Investigating any incidents or near-misses to determine root causes and prevent recurrence.
4. Fostering a Safety Culture
Creating a culture of safety involves engaging all employees in safety initiatives and encouraging proactive safety behaviours. Key strategies include:
- Leadership Commitment: Ensuring management demonstrates a strong commitment to safety and leads by example.
- Employee Involvement: Involving employees in safety committees and decision-making processes.
- Recognition and Rewards: Recognising and rewarding safe behaviours and contributions to a safe work environment.
How Trace Consultants Can Help
Optimising warehouse design, automation, workflows, and safety requires expertise and strategic planning. Trace Consultants, a leading supply chain consulting firm, offers comprehensive solutions to help organisations achieve operational excellence in their warehousing operations.
1. Warehouse Design Services
Trace Consultants provides end-to-end warehouse design services, from initial assessment and layout planning to implementation. Their experts ensure that the warehouse design aligns with the organisation’s operational goals and maximises efficiency and safety.
2. Automation Solutions
With extensive experience in warehouse automation, Trace Consultants helps organisations identify the right automation solutions for their needs. They provide guidance on selecting and implementing technologies such as AS/RS, AGVs, and WMS, ensuring seamless integration with existing systems.
3. Workflow Optimisation
Trace Consultants specialises in optimising warehouse workflows and processes. They conduct detailed assessments to identify inefficiencies and implement lean warehousing principles, slotting optimisation, and advanced picking strategies to enhance productivity.
4. Safety Enhancement
Trace Consultants offers comprehensive safety enhancement services, including safety audits, training programs, and the development of safety protocols. Their experts work with organisations to create a safe working environment that protects employees and ensures compliance with safety regulations.
5. Training and Support
To ensure successful implementation of new systems and processes, Trace Consultants offers comprehensive training and support services. Their training programs equip employees with the skills needed to operate automated systems and maintain efficient and safe workflows.
6. Continuous Improvement
Trace Consultants fosters a culture of continuous improvement by providing ongoing monitoring and support. They help organisations track performance metrics, gather employee feedback, and implement improvements to maintain optimal efficiency and safety.
Warehouse design, automation, workflow optimisation, and safety are critical components of a successful warehousing strategy. By focusing on these areas, organisations can achieve significant improvements in efficiency, cost savings, and customer satisfaction while ensuring a safe working environment.
Trace Consultants, with their expertise in supply chain management, offers valuable support in designing efficient and safe warehouses, implementing advanced automation solutions, optimising workflows, and enhancing safety. By partnering with Trace Consultants, organisations can navigate the complexities of modern warehousing and achieve operational excellence in an increasingly competitive market.